In today’s competitive industrial landscape, efficiency and safety are no longer optional—they are essential. Whether in stone fabrication, glass processing, logistics, or manufacturing, companies continually seek smarter ways to manage their material handling processes. One of the most impactful investments available is a vacuum lifter—a specialized, motorized tool that revolutionizes how companies lift, move, and position materials.
But when should a company invest in a material handling equipment vacuum lifter for their production line? This article explores the operational signs, industry use cases, and expert insights that help determine the right time to make the switch from manual to motorized lifting systems.
👉 What Is Material Handling?
👉 What Does Material Handling Mean?
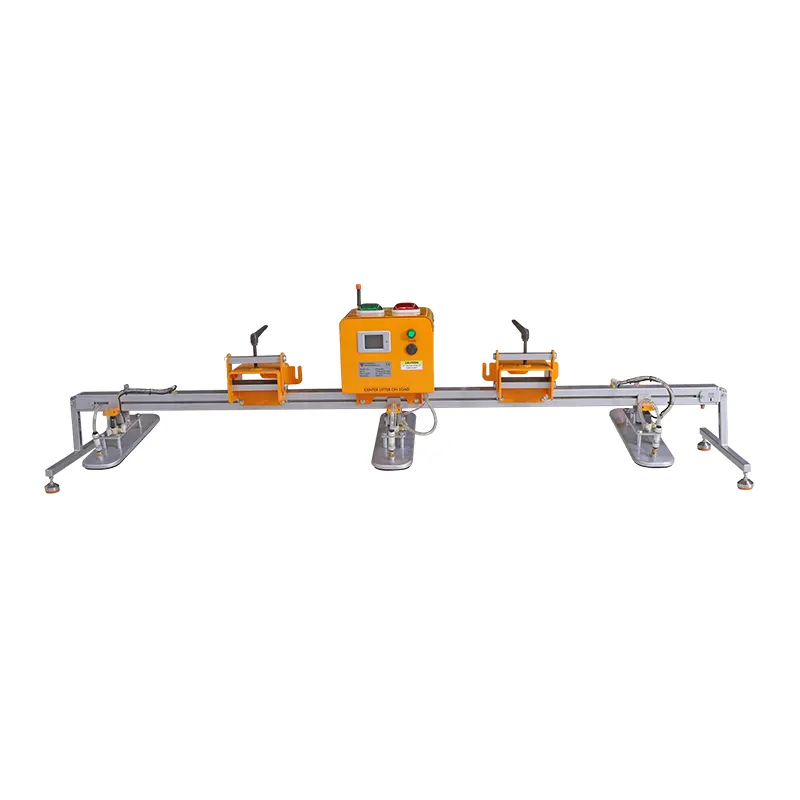
Table of Contents
ToggleUnderstanding Vacuum Lifters in Material Handling
A vacuum lifter is a motorized device that uses suction pads and a vacuum pump to lift non-porous materials—like glass, stone, or sheet metal—safely and securely. They’re often mounted on jib cranes, gantry cranes, or forklifts and serve as powerful alternatives to manual lifters and clamps.
👉 What Is a Material Handling Equipment Vacuum Lifter?
👉 Vacuum Lifters
E-E-A-T: Why This Guidance Matters
✅ Experience
Vacuum lifters have been used in diverse industries—from stone fabrication in Italy to glass handling in the Middle East—for over two decades. Their performance has been proven across various production environments.
✅ Expertise
Engineered by professionals in industrial automation and mechanical design, vacuum lifters are optimized for reliability, safety, and ergonomics.
✅ Authoritativeness
Top manufacturers such as Aardwolf offer certified vacuum lifting equipment trusted by global brands, contractors, and facility managers.
✅ Trustworthiness
Vacuum lifters are built with built-in safety features like pressure alarms, backup tanks, and anti-drop locks, ensuring operational safety and compliance.
Key Signs It’s Time to Invest in a Vacuum Lifter
1. Frequent Handling of Heavy or Fragile Materials
If your production line involves large, heavy, or easily damaged items—such as polished stone slabs, glass panels, or sheet metal—it’s time to move beyond manual material handling.
👉 Which of the Following Is Manual Material Handling?
👉 Which Is an Example of Manual Material Handling Equipment?
2. Labor Costs Are Climbing
Manual lifting typically requires 2–3 workers per item. With a vacuum lifter, one trained operator can handle loads safely and efficiently.
- ✅ Reduce labor cost in construction
- ✅ Free up staff for value-added tasks
3. Injury Rates or Insurance Claims Are Increasing
Repetitive strain injuries from lifting are a major source of downtime and insurance claims. Vacuum lifters reduce direct human contact with loads, significantly enhancing workplace ergonomics.
👉 When Handling Hazardous Materials, You Should?
Benefits of Vacuum Lifters for Production Efficiency
✔ Increase Construction Productivity
Vacuum lifters enable one-person operation and fast cycle times. They’re particularly effective when integrated with conveyors in construction, CNC machines, or assembly lines.
✔ Improve Safety on Construction Site
With controlled vertical and horizontal lifting, vacuum lifters lower accident risk and protect workers and materials.
✔ Minimize Material Waste
Vacuum suction avoids clamping or surface contact, reducing chips, cracks, and scrapes on high-value materials.
Where Vacuum Lifters Fit in the Material Handling Ecosystem
They complement and sometimes replace:
- Forklifts for construction
- Hoists and cranes
- Wheelbarrows, pallets, and carts
- Manual rigging systems
ROI Consideration: When Vacuum Lifters Pay Off
Investing in a vacuum lifter makes strong financial sense when:
- Daily lifting exceeds 500 kg/hour
- Multiple operators are required for manual lifts
- Products damaged during handling cause losses
- Safety violations or injury-related absences are frequent
Most companies achieve full ROI in less than 12 months through labor savings and increased throughput.
👉 Why Is Material Handling Equipment Vacuum Lifter Considered More Efficient Than Manual Lifter?
How to Choose the Right Vacuum Lifter
Factors to evaluate:
- Material surface (smooth, textured, porous)
- Load weight and dimensions
- Vertical vs. horizontal lifting needs
- On-site space constraints
- Integration with existing jib cranes or gantry systems
Industry Examples: Where Vacuum Lifters Shine
Industry | Application |
---|---|
Stone Fabrication | Lifting granite and quartz slabs with precision using Aardwolf Slab Lifters or vacuum pads |
Glass Manufacturing | Non-contact handling of large panels for safety and clarity |
Metal Fabrication | Moving steel, aluminum, or composite sheets |
Logistics & Warehousing | Fast loading/unloading of packaged goods |
Construction Sites | Positioning facade panels and countertops |
When Not to Invest (Yet)
While vacuum lifters offer numerous advantages, they may not be necessary if:
- You only handle small loads (under 50 kg) occasionally
- The material is porous and cannot form a seal with suction pads
- Your workspace doesn’t yet support integration with overhead lifting systems
In these cases, explore other material handling equipment options first.
Final Thoughts: Timing Is Everything
So, when should a company invest in a material handling equipment vacuum lifter?
- When manual lifting is slowing your operations
- When worker safety and productivity are declining
- When your products are damaged due to outdated handling methods
- When your workload and cost projections show the ROI makes sense
Vacuum lifters are not just a luxury—they are a strategic upgrade to any production line that values efficiency, safety, and scalability.
Learn More and Take the Next Step
Explore advanced lifting solutions with:
And expand your knowledge base:
👉 What Is Material Handling Equipment
👉 Material handling Equipment
Please log in to leave a comment.