Material handling cost is one of the most critical—and often underestimated—components of a company’s operational expenses. Whether you operate a warehouse, logistics hub, manufacturing facility, or construction site, understanding the costs involved in moving, storing, and managing materials is vital for optimizing your supply chain and reducing unnecessary spending.
This article breaks down the definition of material handling cost, explains how it’s calculated, identifies what factors influence it, and outlines how to reduce it using efficient systems, training, and modern material handling equipment.
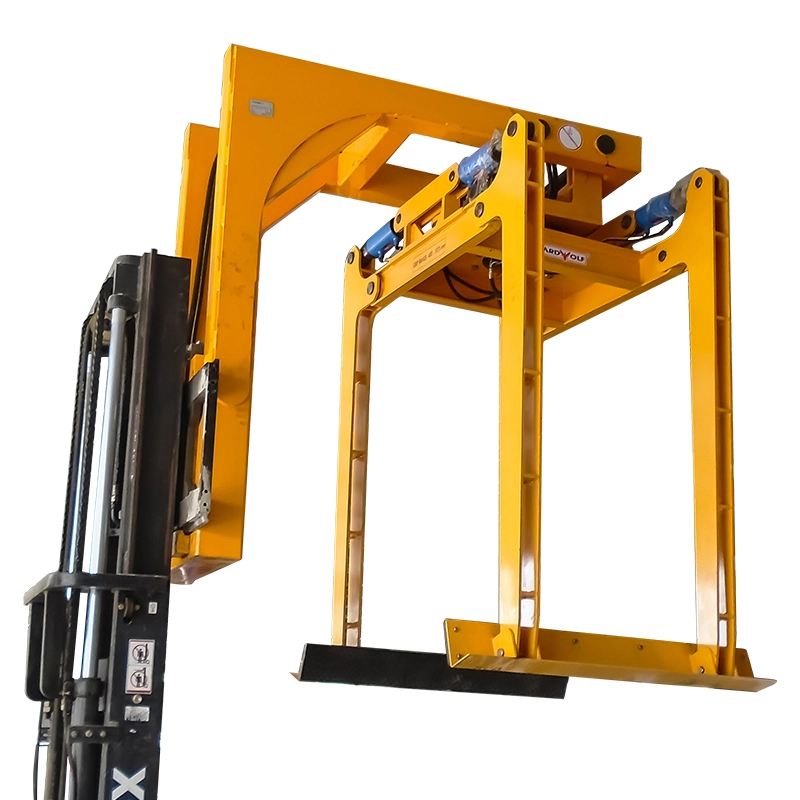
Table of Contents
ToggleWhat Is Material Handling Cost?
Material handling cost refers to all expenses associated with the movement, storage, protection, and control of materials—whether raw materials, components, or finished goods—within a facility or between locations.
These costs typically include:
- Labor (manual or automated)
- Equipment operation and maintenance
- Space utilization
- Energy consumption
- Downtime and inefficiency
- Material damage and loss
Even seemingly minor inefficiencies—like repeated handling of the same materials—can add up to thousands of dollars per month.
Key Components of Material Handling Cost
1. Labor Costs
One of the most significant contributors to material handling cost is labor. This includes:
- Wages for workers operating manual material handling tools
- Staff involved in loading/unloading, sorting, and internal transport
- Lost productivity due to fatigue or injury
🔗 How Does Material Handling Impact the Human Labor Force?
2. Equipment Costs
Costs include purchasing, leasing, or maintaining tools and machinery such as:
- Forklifts for material handling
- Conveyors for material handling
- Warehouse material handling equipment
- Lifting clamps for vertical and angled loads
🔗 lifting clamps - Vacuum lifters and slab lifters for handling stone and glass
🔗 Vacuum Lifters
🔗 Aardwolf Slab Lifters
3. Space and Facility Utilization
Inefficient facility layouts increase walking, driving, or lift times, leading to higher costs. Unused vertical space or poor shelf planning increases rent or real estate requirements.
Modern solutions like overhead material handling systems and bulk material handling systems help maximize floor area and cut unnecessary motion.
🔗 What Is Bulk Load in Material Handling?
4. Material Damage and Loss
Breakage, mishandling, and improper storage can result in lost inventory, repairs, or replacements—all of which inflate handling costs. Investing in proper tools like paver lifters for outdoor sites ensures safer transport.
5. Energy and Downtime
High energy use from inefficient or outdated industrial material handling solutions contributes to higher costs, as does unexpected downtime from equipment failure or workflow delays.
How to Calculate Material Handling Cost
A simple calculation is:
Material Handling Cost = (Labor + Equipment + Facility + Damage + Downtime + Energy) ÷ Number of Units Moved
Example:
- Monthly Labor = $12,000
- Equipment maintenance = $3,000
- Energy & space = $2,000
- Material losses = $1,000
- Units handled = 10,000
Cost per unit = $18,000 / 10,000 = $1.80 per unit
Factors That Influence Material Handling Costs
✅ Volume and Weight of Materials
Heavy or irregular loads often require specialized tools like cranes and hoists, increasing costs.
✅ Type of Handling: Manual vs Automated
Automated material handling systems reduce labor over time but come with higher upfront investment.
🔗 Benefits of Automated Material Handling Systems
✅ Industry-Specific Demands
- Material handling in logistics requires fast throughput.
- Material handling in construction demands rugged tools like jib cranes.
- Material handling in food industry must meet strict hygiene regulations.
- Pharmaceutical material handling systems require precision and contamination-free processes.
Strategies to Reduce Material Handling Cost
1. Optimize Facility Layout
Redesign flow paths to minimize unnecessary movement. Use:
- Material handling carts and trolleys
- Overhead conveyors
- Warehouse zoning to group related activities
2. Use the Right Equipment
Avoid misapplication of tools. Choose the best material handling equipment for warehouses based on your operations. This might include:
- Forklifts for palletized goods
- Lifting clamps for irregular stone blocks
- Vacuum systems for fragile materials
3. Automate Where Appropriate
Use automated material handling systems like conveyors or robotic arms to:
- Eliminate repetitive tasks
- Improve speed and accuracy
- Reduce reliance on manual labor
4. Buy Used or Lease Equipment
Look for used material handling equipment for sale or leasing programs from trusted material handling equipment manufacturers to save capital.
5. Train Your Workforce
Trained staff move materials faster, reduce waste, and avoid injuries. Provide:
- Material handling training programs
- Ergonomic training and best practices
- Safety gear and dress code compliance
🔗 Loose Clothing Is Best to Wear When Handling Material?
Material Handling Cost Across Industries
Industry | Common Tools | Unique Cost Drivers |
---|---|---|
Logistics | Conveyors, forklifts | Speed and volume |
Construction | Cranes, hoists, clamps | Outdoor conditions, load size |
Food | Stainless systems, sealed conveyors | Hygiene and temperature control |
Pharma | Isolated bulk systems, vacuums | Contamination risk, compliance |
Conclusion: Track, Analyze, Optimize
Material handling cost is a key performance indicator for warehouse managers, supply chain specialists, and operations teams. Monitoring and optimizing these costs can directly improve profitability and help scale operations efficiently.
By understanding the core drivers and implementing smart equipment and layout changes, businesses can stay competitive while ensuring a safe, productive workplace.
Please log in to leave a comment.