Material handling costs play a crucial role in operational efficiency and profit margins for businesses involved in warehousing, logistics, manufacturing, and construction. Whether you’re using automated material handling systems or manual material handling tools, understanding how to calculate these costs can help optimize budgets and improve process performance.
In this guide, we break down all the components of material handling cost, calculation methods, and strategies to minimize expenses—making it easier to manage your business operations effectively.
🔗 What Is Material Handling? Types, Equipment, Functions, Safety, and Warehouse Optimization
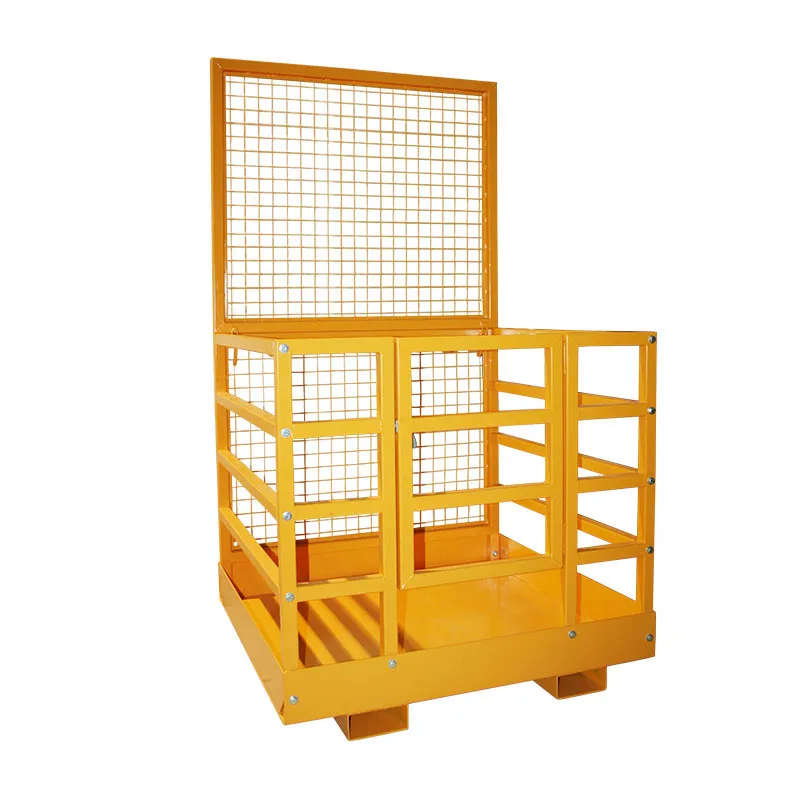
Table of Contents
ToggleWhy Material Handling Cost Matters
Every time a product is moved—be it through conveyors, forklifts, or manual carts—you incur a cost. These costs include labor, equipment depreciation, energy consumption, time delays, and even maintenance expenses. By accurately calculating material handling cost, you can:
- Identify inefficiencies
- Reduce waste
- Improve delivery times
- Lower operational expenses
- Make smarter equipment investments
🔗 How Does Material Handling Impact the Human Labor Force?
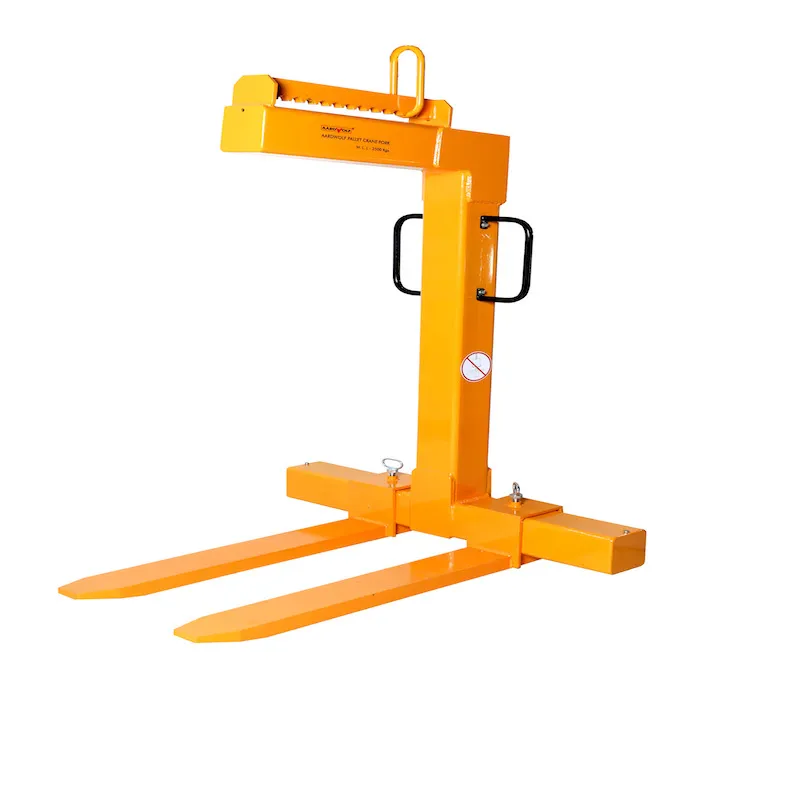
Components of Material Handling Cost
To calculate material handling costs effectively, you need to consider both direct and indirect costs. Here’s a breakdown:
1. Labor Costs
This includes wages, benefits, and training for workers involved in:
- Operating forklifts for material handling
- Using manual material handling tools
- Supervising automated material handling systems
2. Equipment Costs
Calculate expenses for:
- Purchasing or leasing material handling equipment
- Maintenance and repairs
- Insurance and licensing
Useful tools include:
3. Facility Costs
Includes storage space usage, racking systems, and energy consumed by:
- Warehouse material handling equipment
- Overhead material handling systems
- Climate control for sensitive materials like pharmaceutical material handling systems
4. Time-Based Costs
Time is money. The more time spent moving materials, the higher your cost. Consider:
- Travel distance between workstations
- Loading/unloading time
- Setup or adjustment time
Formula to Calculate Material Handling Cost
Here’s a simplified formula to start with:
Material Handling Cost = (Labor Cost + Equipment Cost + Facility Cost + Time-Based Cost) / Volume of Material Moved
Example:
If your monthly expenses are:
- Labor = $10,000
- Equipment = $5,000
- Facility & Energy = $3,000
- Time-Delay Equivalent = $2,000
And you handle 1,000 tons of material,
Material Handling Cost = ($10,000 + $5,000 + $3,000 + $2,000) / 1,000 = $20/ton
This is your per-ton handling cost.
Factors That Affect Material Handling Cost
1. Type of Equipment
Automated systems have a higher upfront cost but lower recurring labor expenses. Manual tools are cheaper but labor-intensive.
2. Material Type
Fragile, heavy, hazardous, or bulk materials demand specialized tools and safety gear.
🔗 Loose Clothing Is Best to Wear When Handling Material?
3. Volume and Frequency
Frequent, high-volume operations benefit more from automated material handling systems like conveyors and robotic sorters.
How to Reduce Material Handling Costs
1. Use the Right Equipment
Choosing efficient tools like paver lifters, forklifts, or cranes and hoists can reduce labor hours and increase throughput.
🔗 How to Use Ratchet Tie Down Straps
🔗 paver lifter
2. Optimize Layout and Storage
Shorter travel distances between workstations reduce time and energy costs. Use vertical space with proper warehouse material handling equipment.
3. Invest in Automation
Implement automated vs manual material handling strategies with smart conveyors, sensors, and AI to cut long-term costs.
4. Training and Safety
Well-trained staff perform faster and reduce downtime due to injuries.
🔗 Material handling training programs
Cost Optimization Across Industries
Material Handling in Construction
Efficiency is key due to time-sensitive projects. Use durable equipment suited for outdoor and rugged environments.
Material Handling in Logistics
Automated sorting, conveyor belts, and barcode scanners streamline large-scale package movement.
Material Handling in Food Industry
Costs increase if hygiene protocols are not met. Stainless steel equipment and quick-clean solutions are ideal.
Pharmaceutical Material Handling Systems
Requires temperature-controlled environments and accurate tracking, adding to overhead costs.
Used Equipment: A Budget-Smart Option
For small businesses, low-cost material handling solutions for small businesses like used material handling equipment for sale can dramatically reduce upfront costs while still offering reliability.
Also explore local options like material handling companies near me and verified material handling equipment manufacturers.
Conclusion
Calculating material handling cost involves more than just equipment prices—it’s a multi-layered process that encompasses labor, time, energy, and infrastructure. Understanding this cost empowers you to:
- Identify operational inefficiencies
- Select appropriate material handling systems
- Improve profit margins
- Scale more confidently
With the right strategies and equipment, businesses across manufacturing, logistics, food processing, and construction can keep costs low while optimizing productivity.
Please log in to leave a comment.