When it comes to material handling, safety is paramount—especially when dealing with hazardous materials. From corrosive chemicals and flammable liquids to biohazards and compressed gases, improper handling can lead to severe health risks, property damage, and environmental contamination. This makes understanding safe handling methods not just good practice, but a legal and ethical necessity.
In this guide, we’ll explore which is a method for the safe handling of hazardous material, backed by industry standards and enhanced by smart tools like material handling equipment, automated material handling systems, and well-planned procedures. This article also integrates essential related keywords and helpful resources for optimal SEO and utility.
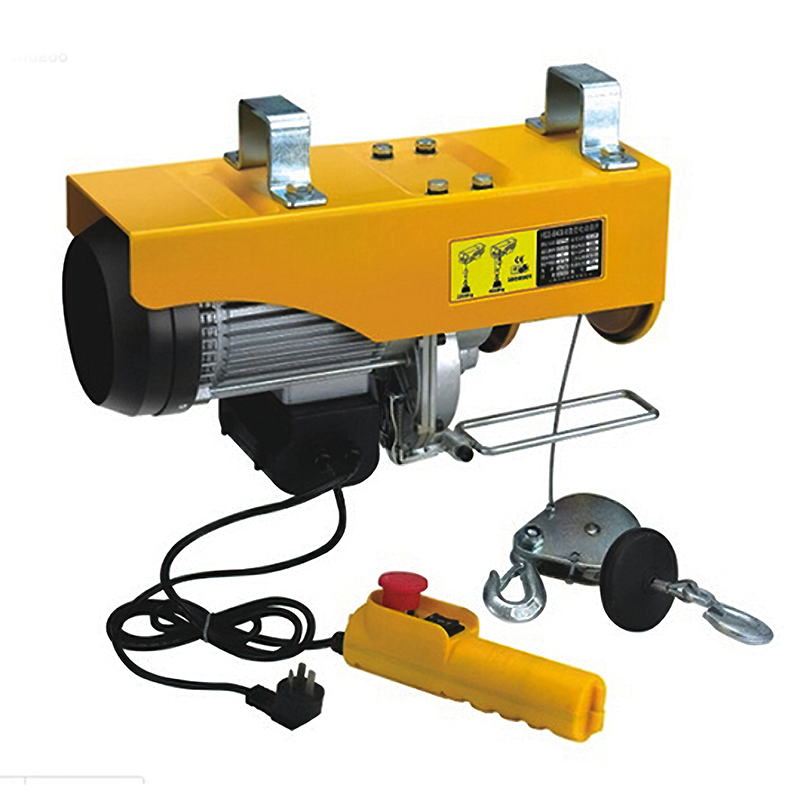
Table of Contents
ToggleWhat Is Material Handling and Why Safety Matters
Material handling refers to the movement, protection, storage, and control of materials—whether hazardous or non-hazardous—throughout their lifecycle within a facility. It includes tools and systems such as:
- Manual material handling tools (e.g., trolleys, pallet jacks)
- Automated material handling systems (e.g., conveyors, robotic lifters)
- Overhead material handling systems (e.g., jib cranes and hoists)
- Bulk material handling systems (for powders, liquids, or granules)
For a foundational understanding, visit:
👉 What Is Material Handling? Types, Equipment, Functions, Safety, and Warehouse Optimization
When hazardous materials are involved, special attention is required to protect employees, equipment, and the environment.
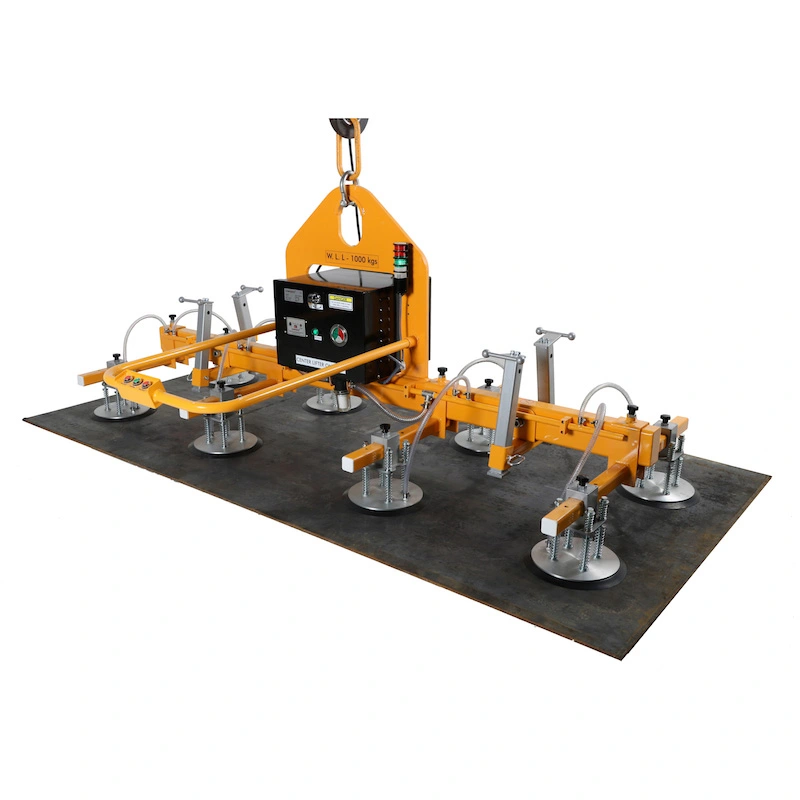
Why Hazardous Materials Demand Special Handling Methods
Hazardous materials are substances that pose a risk to health, safety, property, or the environment. These materials include:
- Flammable or combustible liquids
- Corrosive acids
- Compressed gases
- Radioactive materials
- Pathogens (in pharmaceuticals or healthcare)
Each of these demands a unique industrial material handling solution and proper training to prevent accidents.
Most Effective Methods for the Safe Handling of Hazardous Material
✅ 1. Use of Proper Material Handling Equipment
Using specialized material handling equipment minimizes human contact and exposure. For hazardous loads, consider:
- Vacuum lifters for chemical drums or sensitive components
👉 Explore Vacuum Lifters - Jib cranes and hoists for secure overhead lifting
👉 Check Jib Cranes - Material handling carts and trolleys for transporting smaller quantities safely
Proper tools reduce the risk of spills, drops, or bodily harm.
✅ 2. Employee Training and Certification
No system is safe without competent people operating it. Material handling training programs must include:
- Hazard identification
- Emergency procedures
- Correct use of PPE (Personal Protective Equipment)
- Equipment-specific protocols
Read: How Does Material Handling Impact the Human Labor Force?
Training is especially crucial in environments like material handling in construction, manufacturing, or logistics, where varied hazards exist.
✅ 3. Labeling and Documentation
Every container of hazardous material must be clearly labeled with:
- Hazard classification
- Handling instructions
- Storage requirements
Accompany this with a Material Safety Data Sheet (MSDS) to provide detailed chemical information to the handler.
✅ 4. PPE (Personal Protective Equipment) Enforcement
All workers should wear task-appropriate gear, which may include:
- Gloves resistant to corrosive chemicals
- Respirators for airborne toxins
- Flame-resistant clothing for flammables
Avoid wearing items that can get caught in automated material handling systems or conveyors for material handling.
👉 Loose Clothing Is Best to Wear When Handling Material?
✅ 5. Use of Automated Handling Where Possible
Automated vs manual material handling systems are a crucial choice when safety is the goal. Automation can:
- Reduce human exposure to toxins
- Maintain consistent handling procedures
- Operate in sealed environments (important in pharmaceutical material handling systems)
Learn more about the Benefits of Automated Material Handling Systems.
✅ 6. Designated Hazard Zones and Smart Facility Design
Every facility should establish:
- Designated hazardous material zones
- Clear signage and floor markings
- Airflow controls for ventilation
These are part of smart material handling system design considerations, contributing to both safety and operational efficiency.
✅ 7. Spill Response and Containment Systems
Accidents can happen. Ensure your warehouse or plant has:
- Spill kits available at key locations
- Emergency showers and eyewash stations
- Secondary containment for liquid chemicals
This is especially critical in material handling for warehouses dealing with flammable or corrosive materials.
✅ 8. Temperature and Environment Controls
Many hazardous substances require specific temperature or humidity conditions. Failure to monitor environmental factors can result in combustion, explosion, or deterioration.
In material handling in food industry or bulk material handling systems, climate control isn’t optional—it’s essential.
✅ 9. Routine Equipment Maintenance
Neglecting equipment maintenance is a common cause of accidents. Faulty cranes, worn-out forklifts, or leaky valves can turn a safe operation into a hazardous one.
Explore safe and certified options, including used material handling equipment for sale from trusted suppliers.
✅ 10. Regular Safety Audits and Compliance Checks
Compliance with national and international material handling safety standards ensures the long-term safety of your operation. Partner with reliable material handling companies near me to conduct periodic audits.
Bonus: One Method That Should Be Avoided
🚫 “Assume Small Quantities Pose No Risk”
This is not a safe handling method. Even small quantities of hazardous substances can:
- Cause skin burns
- Produce toxic fumes
- Trigger allergic reactions
Always treat all quantities with the same level of respect and safety planning.
Sector-Specific Safe Handling Considerations
🏗️ Material Handling in Construction
Use cranes and hoists or vacuum lifting systems to minimize manual handling of adhesives, flammable sealants, and heavy containers.
🧪 Pharmaceutical Material Handling Systems
Ensure sterile environments, sealed transport, and automation to minimize contamination and worker exposure.
🏭 Material Handling for Manufacturing
Incorporate heavy-duty material handling solutions and robotics for repetitive or high-risk tasks.
🏪 Warehouse Material Handling Equipment
Design floor plans for safe hazardous materials transport with wide aisles and specialized zones.
How to Choose the Right Material Handling System
Choosing the safest system requires analyzing:
- Type of hazardous material
- Frequency of handling
- Storage conditions
- Workforce capabilities
Use this insight to work with expert material handling system suppliers or material handling equipment manufacturers to build a custom solution.
Final Thoughts
If you’re wondering which is a method for the safe handling of hazardous material, remember this: safety is not optional—it’s a systematic approach that combines training, equipment, labeling, and process control.
Whether you’re handling corrosive chemicals in manufacturing, sensitive pharmaceuticals, or volatile materials in logistics, apply:
- The right material handling equipment
- A trained workforce
- Smart facility planning
- Constant vigilance through audits and maintenance
Related Reading & Resources
- What Is Material Handling? Types, Equipment, Functions, Safety, and Warehouse Optimization
- How Does Material Handling Impact the Human Labor Force?
- Loose Clothing Is Best to Wear When Handling Material?
- Slab Lifters
- Vacuum Lifters
- Jib Cranes
- Which Is One of the Most Common Material Handling Accidents?
Please log in to leave a comment.