Slip and trip hazards are some of the most common causes of workplace injuries, particularly in environments involving material handling. Whether lifting a box, operating a forklift, or working near a conveyor system, the combination of moving people, heavy loads, and active equipment creates perfect conditions for accidents.
But just how significant is the connection between material handling and slips, trips, and falls? Studies show that over 25% of workplace slip, trip, and fall incidents occur during material handling tasks, making it one of the leading risk activities in industrial and commercial environments.
In this comprehensive article, we’ll explore this statistic in depth, examine the specific risks tied to material handling, and offer proactive solutions involving material handling equipment, safety training, and operational planning—all while integrating semantic SEO best practices and essential keywords.
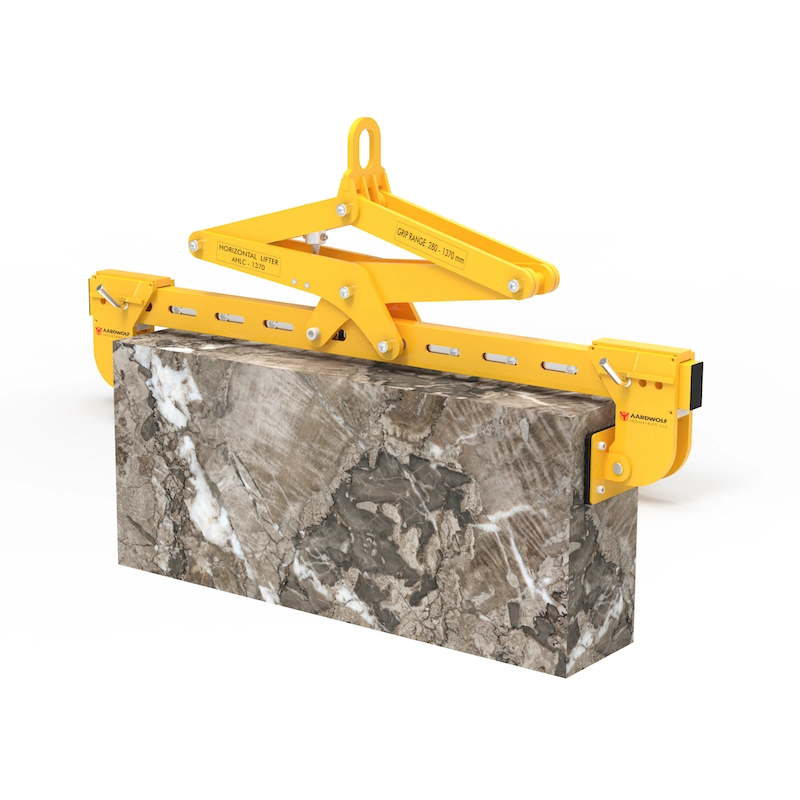
Table of Contents
ToggleWhat Is Material Handling?
Material handling refers to the movement, protection, storage, and control of materials throughout manufacturing, warehousing, distribution, consumption, and disposal. It includes the use of:
- Manual material handling tools such as pallet jacks and hand trucks
- Material handling equipment like forklifts and hoists
- Automated material handling systems like conveyors and robotics
- Bulk material handling systems for powders, liquids, and granular products
Learn more:
👉 What Is Material Handling? Types, Equipment, Functions, Safety, and Warehouse Optimization
Because of the movement of heavy and awkward loads across various surfaces, slips and trips frequently occur—especially in fast-paced industries like material handling in logistics, warehousing, and construction.
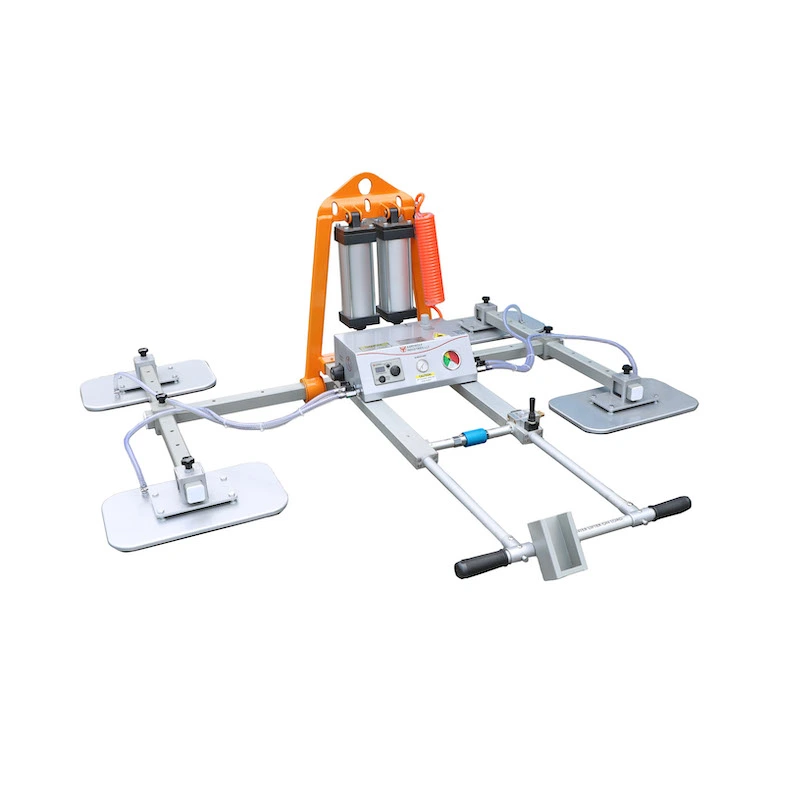
The Data: How Many Slips and Trips Happen During Material Handling?
According to global occupational safety organizations such as OSHA, HSE, and NSC:
- 25–30% of workplace slips and trips occur during material handling tasks
- These accidents often result in strains, sprains, fractures, and long-term musculoskeletal injuries
- They are especially common in industries relying on manual handling, forklifts, and overhead material handling systems
This aligns with OSHA’s broader statistic that slips, trips, and falls account for 15% of all accidental deaths, second only to motor vehicles.
So, when you’re handling materials, whether manually or mechanically, you’re in one of the highest-risk zones for these types of injuries.
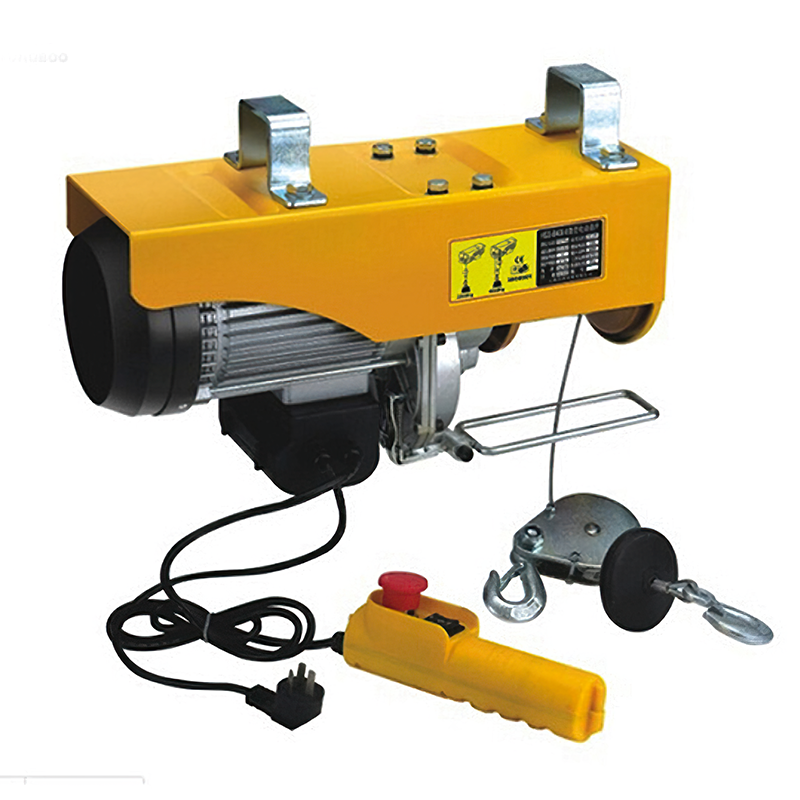
Why Are Slips and Trips So Common in Material Handling?
1. Wet or Oily Floors in Handling Zones
In operations like material handling in food industry or pharmaceutical material handling systems, spills can quickly lead to slick surfaces.
2. Obstructed Walkways and Aisles
Pallets, packaging, and material handling carts and trolleys left in high-traffic areas often become tripping hazards—especially in warehouse material handling environments.
3. Poor Lighting in Storage or Loading Areas
Low visibility makes it difficult for workers to see uneven surfaces, spilled materials, or protruding equipment like conveyors or bulk containers.
4. Inappropriate Footwear and PPE
Improper footwear lacking grip, or loose clothing that catches on equipment, contributes to slips and falls.
👉 Loose Clothing Is Best to Wear When Handling Material?
Real-World Examples by Industry
🏗️ Material Handling in Construction
- Uneven surfaces and outdoor weather conditions create slipping hazards when moving bulk materials
- Workers often operate cranes and hoists, which require stable footing and balance
🏭 Material Handling for Manufacturing
- Oils and lubricants from machinery often leak onto walking paths
- Handling of raw materials using heavy-duty material handling solutions increases risk of sudden spills
🧪 Pharmaceutical and Food Processing Facilities
- Hygienic requirements involve frequent cleaning, resulting in wet surfaces
- Automated material handling systems reduce manual labor but don’t eliminate floor hazards
Solutions: How to Reduce Slip and Trip Hazards During Material Handling
✅ 1. Invest in the Right Equipment
Choose the best material handling equipment for warehouses or your specific industry to minimize manual contact and control load movement.
Examples include:
- Vacuum lifters for smooth transport of fragile or heavy materials
- Aardwolf slab lifters to reduce worker fatigue and increase load security
- Jib cranes and gantry cranes for vertical lifting in restricted spaces
✅ 2. Maintain Clean and Clear Work Areas
- Implement strict housekeeping protocols
- Mark designated areas for forklifts for material handling and pedestrian walkways
- Use spill-containment tools and slip-resistant floor coatings
✅ 3. Train Workers with Real-World Scenarios
Offer scenario-based training as part of your material handling training programs that includes:
- Identifying slip and trip hazards
- Using PPE appropriately
- Reporting and responding to floor hazards in real-time
✅ 4. Wear Appropriate PPE
Ensure that workers wear:
- Slip-resistant, steel-toe footwear
- High-visibility clothing in active zones
- Safety harnesses where overhead material handling systems are used
For complete PPE guidance:
👉 What Protective Equipment Is Required When Handling This Material?
✅ 5. Improve Facility Design and Workflow
Well-planned layouts improve not only efficiency but also safety. Key material handling system design considerations include:
- Wider aisles for automated vs manual material handling
- Floor markings and mirrors in blind spots
- Designated storage for used material handling equipment for sale to avoid clutter
Bonus Tip: Combine Safety with Efficiency
Addressing slip and trip hazards also improves productivity. When workers are confident in the stability of their environment and the efficiency of their tools, operations run smoother.
Enhancing safety helps:
- Reduce insurance claims
- Lower employee turnover
- Improve morale
- Meet material handling safety standards
For budget-conscious operations, explore low-cost material handling solutions for small businesses through certified vendors.
Final Thoughts
If you’re asking what percentage of slip and trip hazards occur while handling material, the answer is clear: roughly 25–30%—and that number is too high to ignore.
By understanding how slips and trips are tied to material handling tasks, you can implement strategies that protect your workforce and your bottom line.
Whether you’re operating in a high-volume warehouse, a precision pharmaceutical facility, or a construction site, consider the long-term benefits of:
- Safer equipment choices
- Thoughtful system design
- Comprehensive training and PPE enforcement
Recommended Reading
- What Is Material Handling? Types, Equipment, Functions, Safety, and Warehouse Optimization
- How Does Material Handling Impact the Human Labor Force?
- Loose Clothing Is Best to Wear When Handling Material?
- Aardwolf Slab Lifters
- Vacuum Lifters
- Jib Cranes
- What Protective Equipment Is Required When Handling This Material?
Please log in to leave a comment.