In modern industries—whether in manufacturing, logistics, construction, or pharmaceuticals—sensitive materials and data require strict control and handling procedures. The basis for the storage of classified material handling hinges on legal mandates, organizational protocols, and risk mitigation strategies. From flammable chemicals to proprietary data and regulated materials, safe and secure practices are essential for both compliance and operational safety.
In this article, we dive into the foundational principles that govern classified material handling, explore best practices, and review the material handling equipment and systems that support this critical process.
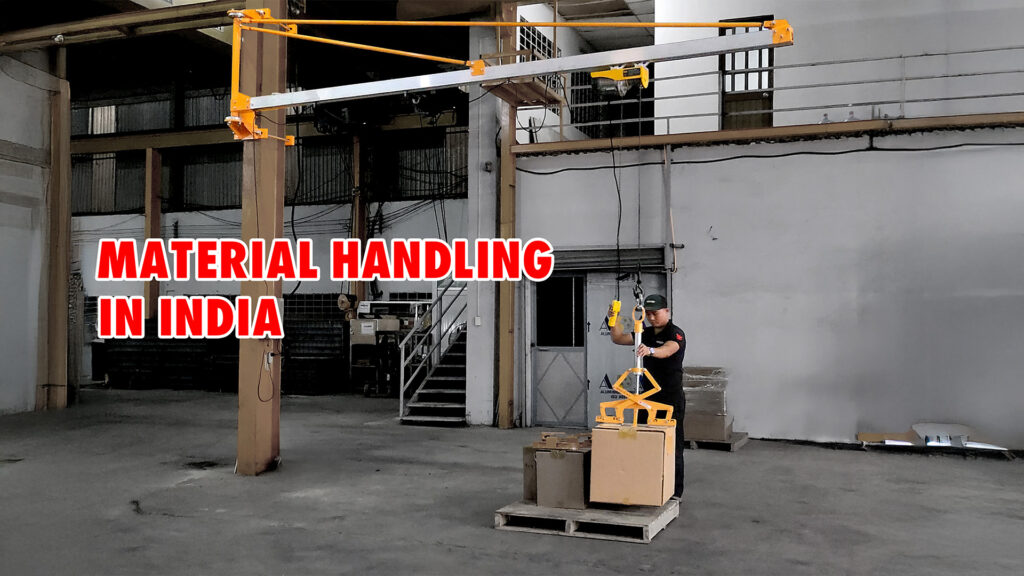
Table of Contents
ToggleUnderstanding Classified Material in Industrial Environments
Classified material in industrial terms refers not only to top-secret files or government intel, but also to:
- Hazardous waste
- Flammable chemicals
- Biohazards
- Pharmaceutical or food-grade materials
- High-value inventory
- Proprietary production components
Each of these must be stored, transported, and accessed in a controlled manner using the right industrial material handling solutions and safety systems.
🔗 What Is Material Handling? Types, Equipment, Functions, Safety, and Warehouse Optimization
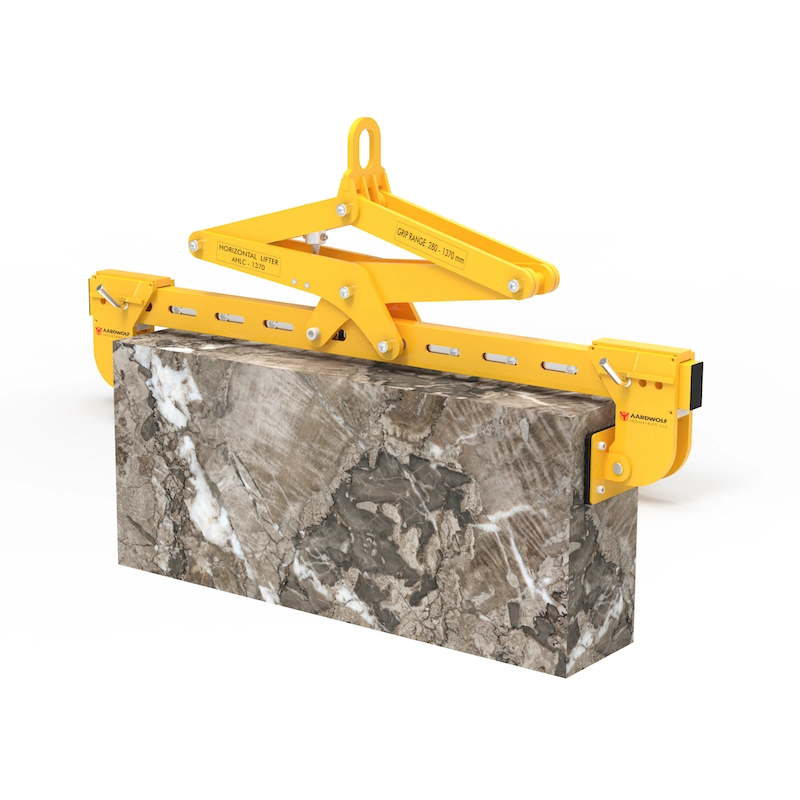
The Legal and Organizational Basis for Classified Material Handling
1. Regulatory Compliance and Industry Standards
The backbone of secure material storage is compliance. Key frameworks include:
- OSHA Hazard Communication Standards
- ISO 45001 (Occupational Health & Safety)
- GMP (Good Manufacturing Practices)
- DOT, EPA, and HAZMAT Regulations for transport and disposal
These guide the use of bulk material handling systems, labeling, inventory logging, and containment for hazardous materials.
2. Material Classification and Risk Assessment
A comprehensive material handling system design begins with classification:
- Toxic
- Reactive
- Flammable
- Biohazardous
- Confidential
Each class determines the storage method, protective equipment, and whether automated material handling systems are preferable over manual material handling tools.
3. Storage Infrastructure and Access Control
One of the key bases for secure handling is controlled access. This involves:
- Restricted zones
- RFID or biometric entry
- Time-tracked access logs
- Surveillance integration
Systems such as warehouse material handling equipment and overhead material handling systems are often equipped with smart tech to regulate access during operation.
🔗 Related: How Does Material Handling Impact the Human Labor Force?
Equipment and Tools for Classified Material Handling
1. Automated vs Manual Material Handling
- Automated material handling systems (AMHS): Best for hazardous, sensitive, or proprietary materials; includes conveyors for material handling, robotic arms, and AGVs.
- Manual material handling tools: For small-batch, controlled access items, or low-risk classified goods.
A well-balanced facility uses both depending on the risk profile.
2. Specialized Handling Tools
For classified or delicate materials, typical equipment includes:
- Vacuum Lifters – touchless lifting that minimizes contamination
🔗 View Aardwolf Vacuum Lifters - Paver Lifters for heavy-duty secure lifting
🔗 Vacuum Paver Lifter AVPL40 - Jib Cranes – controlled motion and extended reach in closed environments
🔗 Aardwolf Jib Cranes - Forklifts for Material Handling with operator cabins and sealed containers
3. Containment and Environmental Controls
Storage units should feature:
- Spill-proof linings
- Temperature and humidity controls
- Fire suppression systems
- Designated hazard zones
These controls are especially vital in material handling for manufacturing, food industry, and pharmaceutical material handling systems.
Safety Protocols for Handling Classified Materials
1. PPE and Handling Protocols
Personnel working with classified materials should follow material handling safety standards and wear suitable PPE. Refer to:
🔗 Loose Clothing Is Best to Wear When Handling Material?
PPE essentials include:
- Full-face respirators
- Chemical-resistant gloves
- High-visibility or protective suits
- Specialized footwear for electrical or biohazard zones
2. Training and Certification
Companies should invest in:
- Material handling training programs
- Annual re-certification for operators
- Regular risk assessments and drills
This is vital for workers in material handling in logistics, construction, and pharmaceutical facilities.
3. Segregation and Redundancy
The storage plan must feature:
- Separate zones for incompatible materials
- Redundant barriers (e.g., dual containment units)
- Backup power for climate-controlled environments
- Emergency response systems
🔗 Aardwolf Slab Lifters are an ideal solution for high-risk slab movement under strict handling conditions.
Smart Systems for Classified Material Management
RFID and Barcode Tracking
Modern systems use RFID tags and barcode scanning integrated into warehouse material handling equipment to track:
- User access
- Duration of exposure
- Environmental data logs
- Maintenance history of equipment
IoT-Based Monitoring
IoT sensors enable real-time monitoring of conditions such as:
- Ambient temperature
- Movement or tampering alerts
- Air quality or chemical levels in storage areas
Such systems support heavy-duty material handling solutions and help meet regulatory compliance effortlessly.
Final Thoughts: Build a Safety-First Culture
The foundation for securely handling and storing classified materials isn’t just about hardware. It requires:
- Company-wide awareness
- Clear documentation and SOPs
- Verified equipment from reliable material handling equipment manufacturers
- Continuous improvements in efficiency and safety
Please log in to leave a comment.