Material handling safety refers to the practices, procedures, and precautions taken to ensure the safe movement, control, storage, and protection of materials throughout the lifecycle of a product—from raw material intake to final distribution. It plays a pivotal role in minimizing injuries, protecting equipment, and maintaining smooth operations across various industries such as warehousing, logistics, manufacturing, food processing, and construction.
As work environments increasingly rely on complex systems like material handling equipment, automated material handling systems, and manual tools, safety becomes more than a regulation—it becomes a necessity.
In this in-depth article, we’ll explore what material handling safety truly means, how to implement it, and why it’s vital for today’s industrial operations.
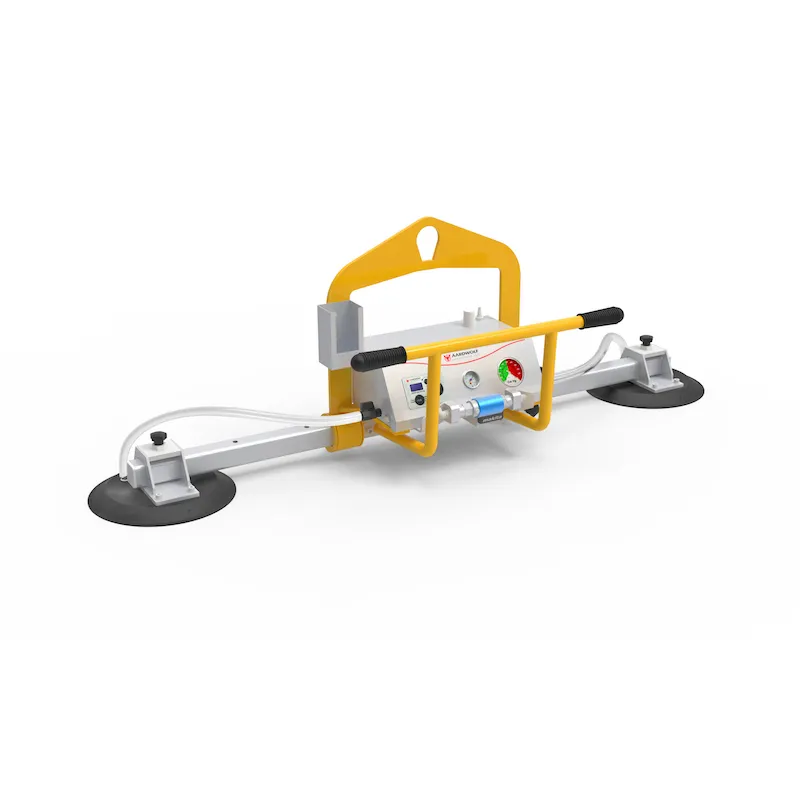
Table of Contents
ToggleUnderstanding the Basics: What Is Material Handling?
Before diving into safety, it’s important to understand the foundation.
Material handling involves the movement, storage, and control of materials using various tools and equipment. This includes:
- Manual material handling tools like trolleys and dollies
- Warehouse material handling equipment such as forklifts and pallet jacks
- Overhead material handling systems like cranes and hoists
- Bulk material handling systems for powders, liquids, and aggregates
To explore the topic in detail, visit:
👉 What Is Material Handling? Types, Equipment, Functions, Safety, and Warehouse Optimization
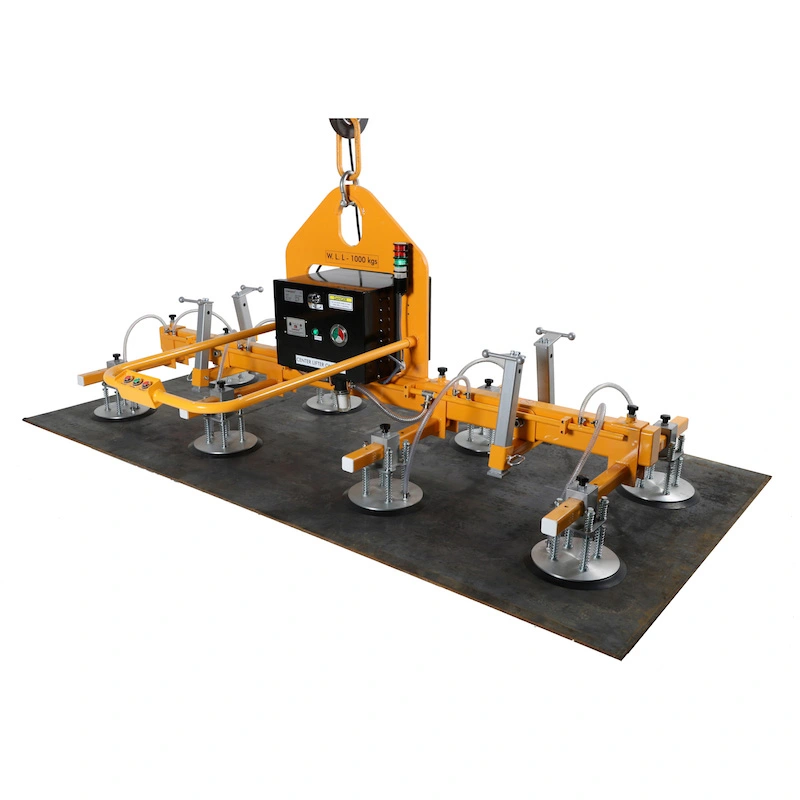
Why Is Material Handling Safety Important?
Every day, thousands of workers face the risk of injury from lifting heavy loads, operating machinery, or moving materials through complex environments. Without proper safety measures, these activities can result in:
- Musculoskeletal injuries
- Slips, trips, and falls
- Crushed limbs from forklifts for material handling or cranes and hoists
- Exposure to hazardous substances in pharmaceutical material handling systems
Implementing material handling safety reduces risks, improves efficiency, and boosts morale across industries.
Common Hazards in Material Handling
1. Improper Lifting Techniques
Manual lifting is a leading cause of workplace injury. Workers lifting with their backs instead of their legs risk severe back strain and long-term damage.
2. Slippery or Uneven Surfaces
Material handling in food industry settings often involves wet surfaces, increasing slip risks.
3. Poorly Maintained Equipment
Broken conveyors, malfunctioning forklifts, or loose components in jib cranes can lead to catastrophic failures.
4. Inappropriate Clothing
Loose clothing can get caught in automated material handling systems or moving equipment.
For more on safe attire, read:
👉 Loose Clothing Is Best to Wear When Handling Material?
Essential Safety Tips for Material Handling
✅ 1. Use the Right Equipment for the Job
Selecting the proper industrial material handling solutions prevents overexertion and mechanical failure. Examples include:
- Vacuum lifters for glass or tile
- Aardwolf slab lifters for stone and concrete
- Paver lifter for landscaping and construction
✅ 2. Prioritize Training and Certification
A well-trained workforce is the cornerstone of safety. Implement ongoing material handling training programs that include:
- Lifting techniques
- Equipment operation
- Emergency procedures
- Hazard communication
✅ 3. Maintain Equipment Regularly
Whether you’re using warehouse material handling equipment or bulk material handling systems, proactive maintenance is critical to avoid breakdowns and accidents.
✅ 4. Apply Safety Standards and Regulations
Comply with material handling safety standards such as OSHA, ISO, or local safety codes. Regular audits help ensure your equipment and practices remain up to date.
✅ 5. Plan Material Flow and Facility Layout
Smart material handling system design considerations can eliminate unnecessary movement, reduce worker fatigue, and enhance productivity. Key factors to address include:
- Aisle width
- Load-bearing capacity
- Storage location relative to dispatch zones
- Clearance for overhead material handling systems
✅ 6. Utilize Automation Where Possible
Automated material handling systems reduce reliance on manual labor, prevent injuries, and increase operational efficiency. These systems are especially effective in:
- Material handling for warehouses
- Material handling in manufacturing
- Pharmaceutical material handling systems
Learn more about the benefits of automated material handling systems.
How Material Handling Safety Varies by Industry
🏗️ Material Handling in Construction
- Use of jib cranes and hoists for vertical lifting
- Ground instability and weather increase risks
- PPE and fall prevention are critical
🏪 Material Handling for Warehouses
- High foot traffic and vehicle use
- Inventory stacking hazards
- Best handled with forklifts, trolleys, and smart layout design
🧪 Pharmaceutical Handling
- Containment is crucial
- Workers must avoid exposure to active substances
- Rely on sealed automated systems and precise PPE protocols
🧱 Material Handling in Logistics
- Fast-paced environments increase risk of collision and injury
- Regular training on safety tips for manual material handling is vital
Advantages of Safe Material Handling Practices
- Reduced workplace injuries and related compensation costs
- Improved productivity through optimized load handling
- Longer equipment lifespan due to correct use
- Stronger compliance with industry regulations
- Higher employee morale in a safe and organized workspace
Selecting the Right System
Every business has unique handling needs. When choosing between automated vs manual material handling, consider:
- Load size and frequency
- Labor availability
- Budget constraints (explore low-cost material handling solutions for small businesses)
- Facility design
For guidance, connect with trusted material handling system suppliers or material handling companies near me.
Final Thoughts
What is material handling safety? It’s the combination of strategic equipment use, staff training, system design, and regulatory compliance that ensures every material-handling task is performed without injury or incident.
From a small packaging line using manual tools to a complex warehouse running automated material handling systems, the principles of safety apply everywhere.
By focusing on smart investments, regular training, and equipment maintenance, businesses can not only protect their workforce—but also gain a competitive edge through smoother, faster, and safer operations.
Please log in to leave a comment.