Material handling safety is essential for maintaining a productive, injury-free workplace. Whether you’re lifting boxes, operating cranes, or using advanced automated material handling systems, adhering to strict safety protocols ensures not only compliance with regulations but also the wellbeing of employees.
According to OSHA and industry best practices, the key to minimizing injury risk lies in a combination of proper equipment, ergonomics, training, and workflow design. Inspired by AdvancedCT’s safety checklist, this guide explores material handling safety requirements that apply across industries—from construction sites and warehouses to food and pharmaceutical environments.
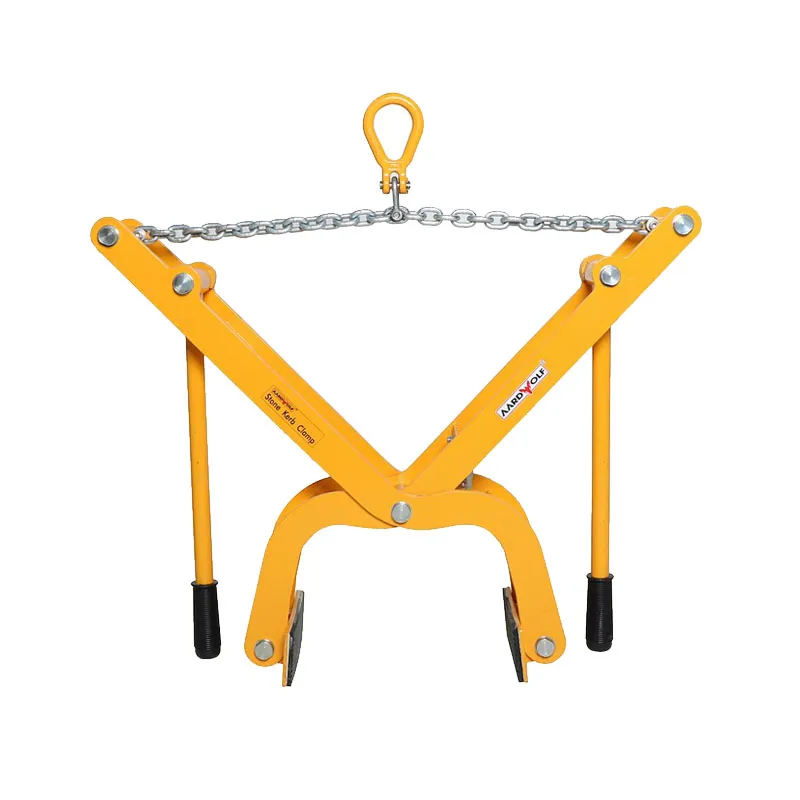
Table of Contents
ToggleWhat Is Material Handling?
Before diving into safety requirements, it’s crucial to understand the fundamentals of material handling.
Material handling involves the movement, protection, storage, and control of products and materials throughout manufacturing, warehousing, distribution, and disposal. It encompasses a wide range of material handling equipment and practices—from manual material handling tools like carts and trolleys to sophisticated bulk material handling systems and conveyors.
👉 What Is Material Handling? Types, Equipment, Functions, Safety, and Warehouse Optimization
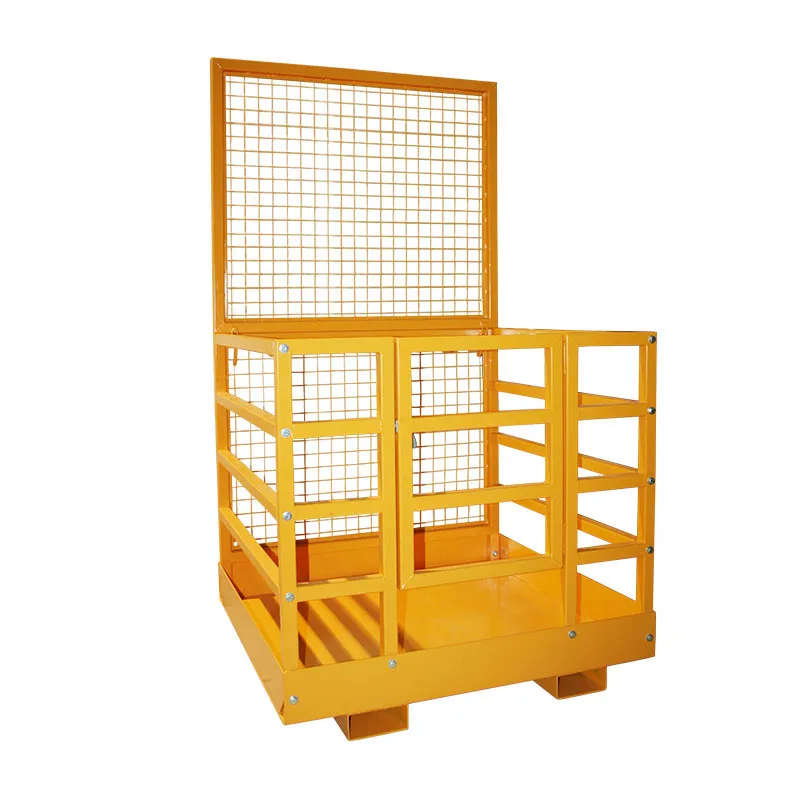
Why Safety in Material Handling Matters
Manual lifting, awkward postures, and improper equipment use are major contributors to workplace injuries, particularly back injuries, sprains, and fractures. Proper material handling safety:
- Reduces injury rates
- Boosts operational efficiency
- Lowers liability and insurance costs
- Improves worker morale and productivity
Check how material handling affects labor:
👉 How Does Material Handling Impact the Human Labor Force?
1. Assess the Load Before Lifting
Before any manual movement, workers should:
- Evaluate the weight and dimensions of the object
- Check for sharp edges, wet surfaces, or unstable packaging
- Use manual handling tools or lifting equipment where needed
If loads exceed safe limits or have irregular shapes, tools like vacuum lifters or Aardwolf slab lifters can help manage them safely.
Explore more:
👉 Examples of Lifting Equipment
2. Use the Right Material Handling Equipment
Each task requires equipment tailored to the load type and operational environment. Common options include:
- Material handling carts and trolleys – for light to moderate loads
- Forklifts for material handling – for palletized goods
- Cranes and hoists – for vertical lifting in confined spaces
- Jib cranes – for precise lifting in tight or repetitive spaces
- Paver lifter – ideal for landscaping or construction material handling
Selecting the best material handling equipment for warehouses or production lines greatly reduces ergonomic strain and risk.
3. Follow Proper Lifting Techniques
Even when using manual material handling tools, workers must use safe lifting postures:
- Keep the back straight and lift with the legs
- Hold the load close to the body
- Avoid twisting or reaching during the lift
- Ensure firm footing and a clear path
Clothing should also be suitable for the task—tight-fitting, non-obstructive, and free from accessories that could get caught.
👉 Loose Clothing Is Best to Wear When Handling Material?
4. Train Staff in Safety Protocols
Material handling training programs are critical. They should cover:
- Identification of load risks
- Proper use of warehouse material handling equipment
- Hazard recognition (spills, obstructions, improper storage)
- Use of lifting equipment and PPE
- Lockout/tagout procedures for automated systems
Trained staff are far less likely to misuse equipment or suffer injuries.
5. Maintain and Inspect Equipment Regularly
Preventative maintenance is a non-negotiable aspect of material handling safety. This includes:
- Inspecting cranes, forklifts, and conveyors for wear
- Lubricating and replacing parts on overhead material handling systems
- Cleaning sensors and filters in pharmaceutical material handling systems
If you’re working on a budget, consider used material handling equipment for sale, but always ensure it meets material handling safety standards.
6. Design an Ergonomic Workflow
Proper material handling system design considerations enhance safety by reducing manual steps and repetitive movements. Factors to consider:
- Reducing unnecessary lifting through better layout
- Storing heavy materials at waist level
- Using automated material handling systems for repetitive or hazardous tasks
- Minimizing walking distance through optimized bulk material handling systems
This also significantly improves material handling efficiency and throughput.
7. Comply with Material Handling Safety Standards
Ensure adherence to standards like:
- OSHA 1910 Subpart N (Materials Handling and Storage)
- ISO 45001 (Occupational Health and Safety)
- Local workplace safety codes and ergonomic guidelines
Documentation, incident tracking, and regular audits help enforce and refine these protocols.
8. Account for Industry-Specific Needs
Different sectors have unique safety considerations:
🏗️ Material Handling in Construction
Irregular terrains and heavy loads demand rugged industrial material handling solutions like cranes and vacuum paver lifters.
🧬 Material Handling in Food and Pharma
Cleanability and contamination control are critical—automated, sealed systems reduce manual exposure.
🏭 Material Handling for Manufacturing
Here, automated vs manual material handling becomes a key decision—automation often boosts safety and efficiency.
📦 Material Handling in Warehouses
High movement frequency demands ergonomics, layout optimization, and smart tools like conveyors for material handling and forklifts.
9. Use Visual Aids and Signage
A visible, easy-to-understand safety communication system prevents confusion and enhances compliance. Use:
- Color-coded zones
- Load rating labels on equipment
- Safety posters and emergency instruction signage
These systems complement formal training and reduce incident frequency.
10. Encourage a Culture of Safety
The most advanced material handling system suppliers will tell you—equipment alone isn’t enough. You must:
- Empower workers to report hazards
- Reward safety improvements
- Encourage proactive safety behavior
- Review incidents and learn from them
Workplace safety is a shared responsibility between management and employees.
Conclusion: Making Safety the Standard
So, what are the safety requirements for material handling? From choosing the right tools to training your staff and optimizing facility layouts, the answer lies in creating a culture where safety is baked into every decision. Proper material handling equipment, knowledge, and vigilance not only prevent injury—they improve operational performance.
If you’re starting or upgrading your safety strategy, begin with reliable tools like vacuum lifters, slab lifters, and ergonomic lifting equipment, and work with experienced material handling equipment manufacturers to design the ideal setup for your industry.
Please log in to leave a comment.