Material handling is central to many industries—whether in warehousing, construction, logistics, or manufacturing. While it’s essential for transporting raw materials, finished products, or hazardous substances, it also introduces numerous risks. Workers on the front lines often experience and report safety hazards that can compromise their well-being and the integrity of the workplace.
This article explores some of the most common material handling hazards as cited by workers, drawing from real-world feedback and backed by practical solutions using proper material handling equipment, safety training, and system optimization.
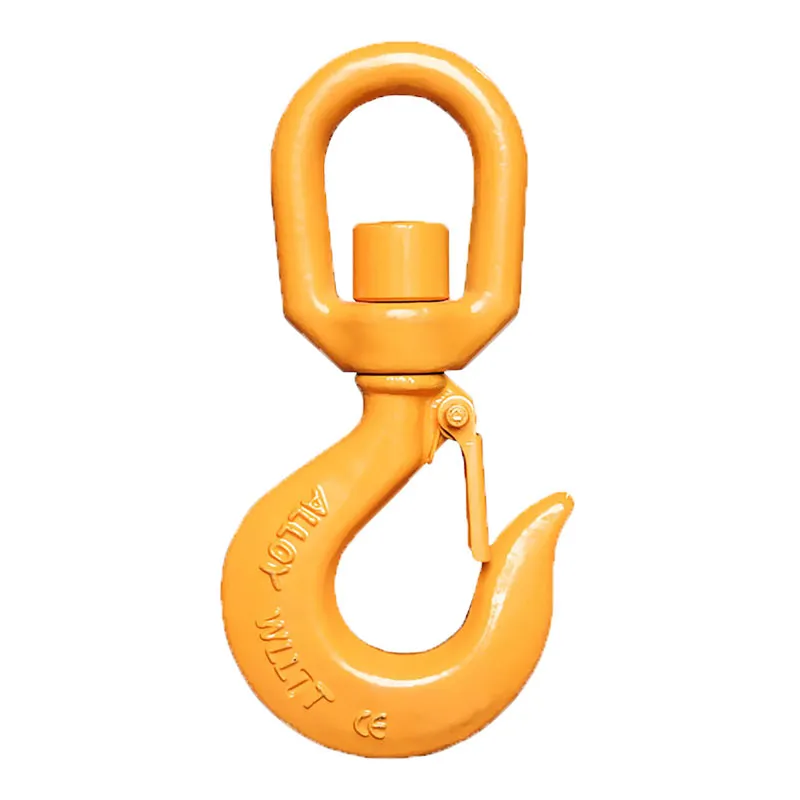
Table of Contents
ToggleUnderstanding Material Handling: The Foundation of Every Safe Workplace
Material handling refers to the movement, protection, storage, and control of materials throughout manufacturing, warehousing, and distribution. It includes:
- Manual material handling tools (e.g., pallet jacks, hand trucks)
- Automated material handling systems (e.g., conveyors, robotics)
- Bulk material handling systems (for liquids, grains, chemicals)
- Overhead material handling systems (e.g., cranes and hoists)
Whether you’re operating in material handling for manufacturing or material handling in logistics, maintaining safety requires understanding risks from the ground up.
👉 Read more:
What Is Material Handling? Types, Equipment, Functions, Safety, and Warehouse Optimization
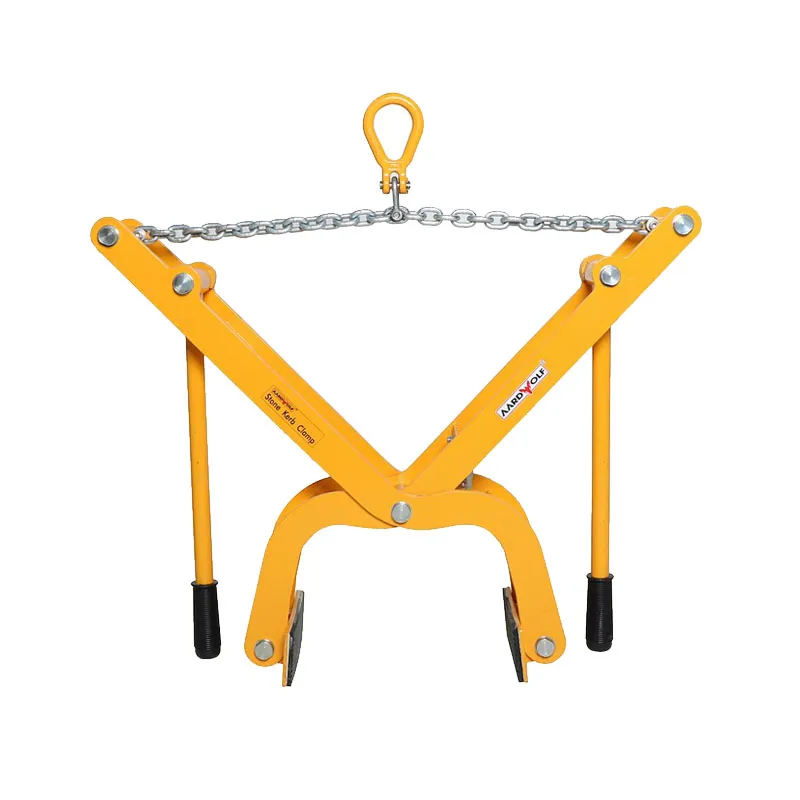
Most Common Material Handling Hazards as Cited by Workers
Let’s examine the hazards most frequently reported by workers and explore how to prevent them through equipment, training, and planning.
1. Improper Lifting Techniques and Overexertion
Overexertion injuries are a top complaint among workers in manual handling environments. Poor lifting posture, lifting too much weight, or repetitive motion can lead to:
- Lower back injuries
- Shoulder and neck strain
- Herniated discs
Prevention Tips:
- Train employees on ergonomic lifting practices
- Provide material handling carts and trolleys for load transport
- Use assistive tools like Aardwolf Slab Lifters to reduce physical strain
2. Inadequate Personal Protective Equipment (PPE)
Improper or missing PPE is another common hazard—especially in material handling in food industry and pharmaceutical material handling systems. Workers often cite discomfort, lack of PPE enforcement, or improper use.
Risks Include:
- Chemical burns
- Cuts or abrasions
- Respiratory exposure
Prevention Tips:
- Provide clear PPE policies and enforcement
- Train workers on selecting and using PPE
- Avoid loose clothing around equipment like conveyors
👉 Loose Clothing Is Best to Wear When Handling Material?
3. Slips, Trips, and Falls
Slippery floors, obstructed pathways, or uneven surfaces near warehouse material handling equipment are a significant source of injuries.
Cited Issues:
- Unsecured cords or packaging debris
- Oil or water spills from bulk storage
- Poor lighting in storage zones
Prevention Tips:
- Mark pedestrian paths clearly
- Use anti-slip flooring and ensure regular cleaning
- Conduct daily walkthroughs to identify hazards
4. Forklift and Crane Incidents
Workers handling forklifts for material handling or cranes and hoists report concerns around:
- Limited visibility
- Inexperienced operators
- Unstable loads
In particular, gantry crane operations require proper training and inspection.
Prevention Tips:
- Conduct regular certification checks for operators
- Use Jib Cranes for safer overhead lifting
- Balance loads and secure with proper slings
5. Poor Equipment Maintenance
Workers frequently report that used material handling equipment for sale or poorly maintained tools can lead to:
- Equipment breakdowns
- Dropped loads
- Delays in operations
Prevention Tips:
- Set a scheduled maintenance calendar
- Replace worn-out parts promptly
- Work with trusted material handling equipment manufacturers
6. Exposure to Hazardous Materials
In bulk material handling systems, improper labeling or container leaks expose workers to chemicals, gases, or biological agents. Workers often cite lack of:
- Safety Data Sheet (SDS) access
- Spill containment systems
- Emergency procedures
Prevention Tips:
- Train employees to read and understand SDSs
- Equip workstations with emergency showers and eyewash stations
- Reference safe practices:
👉 Which Is a Method for the Safe Material Handling of Hazardous?
7. Poor Facility Design and Layout
Material handling system design considerations are often overlooked. Workers struggle with narrow aisles, long transport routes, and overlapping pedestrian/vehicle traffic zones.
Common Complaints:
- Inefficient workflow
- Congestion and collisions
- Time loss and increased fatigue
Prevention Tips:
- Redesign workflows for minimal movement
- Separate zones for pedestrians and forklifts
- Integrate automated material handling systems where possible
8. Lack of Training and Awareness
Untrained workers are more likely to make costly and dangerous mistakes. Many incidents stem from:
- Inability to recognize hazards
- Incorrect use of equipment
- Poor response to emergencies
Solutions:
- Regular material handling training programs
- Visual signage near all equipment
- Role-specific certifications
Industry-Specific Hazards
Material Handling in Construction:
- Uneven terrain
- Heavy structural materials
- Vibration and dust exposure
Material Handling for Warehouses:
- High-volume repetitive lifting
- Forklift-pedestrian interaction
- Limited storage space
Material Handling in Logistics:
- Time pressure for rapid handling
- Night shift hazards
- Dock height mismatches
Pharmaceutical Material Handling Systems:
- Strict contamination controls
- Sealed environments
- Specialized equipment like vacuum lifters
How to Prevent These Hazards: Proactive Measures
✔ Invest in the Best Material Handling Equipment for Warehouses
- Choose durable tools designed for your specific loads
- Implement heavy-duty material handling solutions for bulky items
✔ Leverage Automation Where Possible
- Reduce manual handling using conveyors and robotics
- Compare options in automated vs manual material handling systems
✔ Create a Culture of Safety
- Encourage reporting of near-misses
- Conduct monthly safety audits
- Align with material handling safety standards
Final Thoughts
When asking “What are some of the most common material handling hazards as cited by workers?”, you’re tapping into the real-world experiences of those who face these dangers daily. Their insights point to critical problem areas—manual overexertion, poor training, faulty equipment, and unsafe environments.
To address these challenges:
- Choose the right tools from reliable material handling system suppliers
- Focus on how to improve material handling efficiency through automation and workflow design
- Equip your teams with knowledge, training, and modern safety gear
Your frontline workers are your best safety auditors—listen to them, and you’ll build a workplace that’s not only efficient but truly safe.
Explore More Resources:
- What Is Material Handling? Types, Equipment, Functions, Safety, and Warehouse Optimization
- How Does Material Handling Impact the Human Labor Force?
- Loose Clothing Is Best to Wear When Handling Material?
- Which Is a Method for the Safe Material Handling of Hazardous?
- What Are Some of the Most Common Material Handling Hazards as Cited by Workers?
Need help with optimizing your material handling workflow or equipment? Contact your local material handling companies near me for tailored solutions.
Please log in to leave a comment.