Reducing material handling costs is a key objective for warehouses, logistics centers, construction firms, and manufacturing units. As material handling equipment and labor account for a significant portion of operational budgets, minimizing these costs without compromising productivity or safety is essential for long-term profitability.
In this article, we’ll explore practical strategies to reduce costs across different material handling systems, highlighting cost-saving tips, automation opportunities, and smart equipment usage.
🔗 How to Make My Warehouse Material Handling More Efficient?
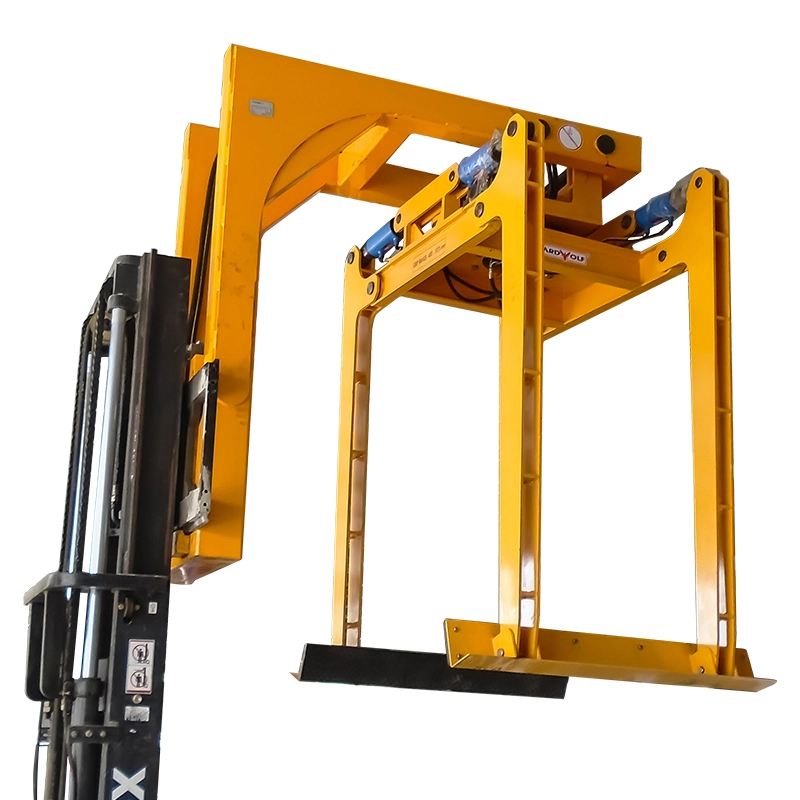
Table of Contents
ToggleUnderstanding the Cost Drivers in Material Handling
Before you can reduce costs, it’s important to know what drives them. These include:
- Equipment acquisition and maintenance
- Labor costs (manual movement, loading/unloading)
- Inefficient workflow or warehouse layout
- Repetitive handling and long travel distances
- Product damage due to improper handling
- Energy consumption of automated material handling systems
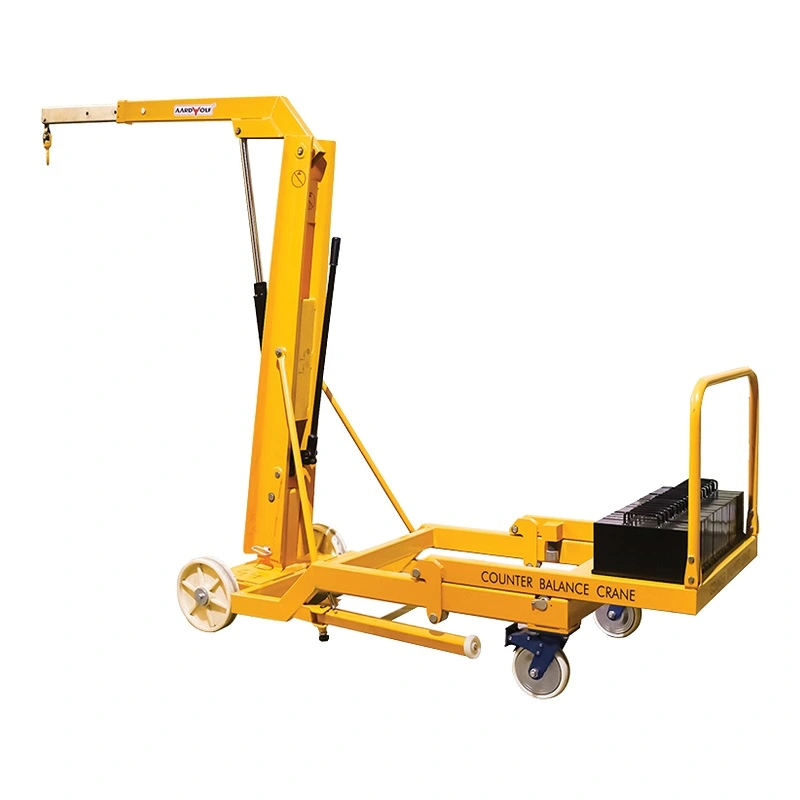
1. Choose the Right Material Handling Equipment
Selecting appropriate material handling equipment tailored to your application can significantly cut down costs by improving efficiency. For example:
- Forklifts for material handling in large storage zones
- Material handling carts and trolleys for internal transport
- Cranes and hoists for heavy loads
- Conveyors for material handling in repetitive movement tasks
- Overhead material handling systems for vertical space utilization
Use multipurpose tools where possible and invest in ergonomic designs to reduce operator fatigue and labor turnover.
2. Invest in Low-Cost and Energy-Efficient Automation
Many businesses hesitate to automate due to upfront costs. However, low-cost material handling solutions for small businesses now offer scalable automation with quick ROI.
Examples include:
- Basic conveyor systems for repetitive tasks
- Robotic palletizers for packing
- Entry-level automated material handling systems
Benefits of automation include:
- Reduced labor cost
- Higher accuracy and consistency
- Improved throughput
3. Optimize Warehouse Layout for Less Travel Time
Poorly organized storage areas increase travel distances, handling time, and operational costs. A well-structured layout can cut material handling effort by up to 40%.
Tips:
- Store high-frequency items near shipping docks
- Use vertical racks and warehouse material handling equipment like jib cranes
- Implement zones for different categories (e.g., hazardous, fragile, bulk)
4. Reduce Manual Handling with Specialized Tools
Repetitive manual lifting increases labor costs and injury risk. Equip your team with:
- Vacuum lifters
- Slab lifters
- Paver lifters
- Specialized suction cup attachments
🔗 suction cup
🔗 Vacuum Lifters
🔗 Paver Lifter
These tools enhance productivity while reducing product damage and employee fatigue.
5. Implement Training Programs
Trained employees move materials more efficiently and safely. Invest in:
- Material handling training programs
- Certifications for forklift operation and hoist use
- Safety modules like:
🔗 Loose Clothing Is Best to Wear When Handling Material?
A skilled team helps reduce costly errors and improves the lifespan of manual material handling tools.
6. Leverage Bulk Handling Where Applicable
Bulk material handling systems eliminate the need for multiple small-item transfers. If you operate in industries like agriculture, mining, or food processing, use:
- Augers
- Elevators
- Bucket conveyors
These systems cut down total handling time and reduce packaging and labor costs.
7. Maintain and Inspect Equipment Regularly
Neglected tools result in breakdowns and downtime. Scheduled maintenance of:
- Material handling carts and trolleys
- Forklifts
- Overhead systems
… can prevent repair expenses and lost productivity. Establish preventive maintenance policies with real-time checklists.
8. Buy Used or Refurbished Equipment
To cut initial costs, small businesses can explore:
- Used material handling equipment for sale
- Leasing options
- Refurbished tools certified by OEMs
Just ensure equipment meets material handling safety standards before purchase.
9. Evaluate Cost Per Movement
Every material movement should add value. Use a simple formula:
Cost per movement = (Labor cost + Equipment usage cost + Energy cost) ÷ Number of units moved
This metric will help you:
- Eliminate redundant movements
- Benchmark productivity
- Choose better industrial material handling solutions
10. Collaborate with Reliable Equipment Manufacturers
Whether you need high-volume pharmaceutical material handling systems or material handling in construction, consult with:
- Reputable material handling equipment manufacturers
- Trusted material handling system suppliers
They offer tailored, long-term solutions based on space, volume, and budget.
Final Thoughts
Reducing material handling cost isn’t about cutting corners—it’s about optimizing efficiency. By investing in the right equipment, improving layout, automating where feasible, and training your workforce, you can reduce operational waste and increase profitability.
Start small—automate one process, upgrade one tool, train one team—and watch your costs decrease over time.
Please log in to leave a comment.