Efficient material handling is essential for businesses working with granite countertops, whether it’s polished, honed, or leathered finishes. Proper practices not only protect heavy and fragile granite slabs for countertops from damage but also enhance workflow, reduce waste, minimize risk, and cut costs.
This guide explores how to improve material handling in the stone industry—from receiving slabs to installation—while applying the latest efficiency techniques and ergonomic best practices.
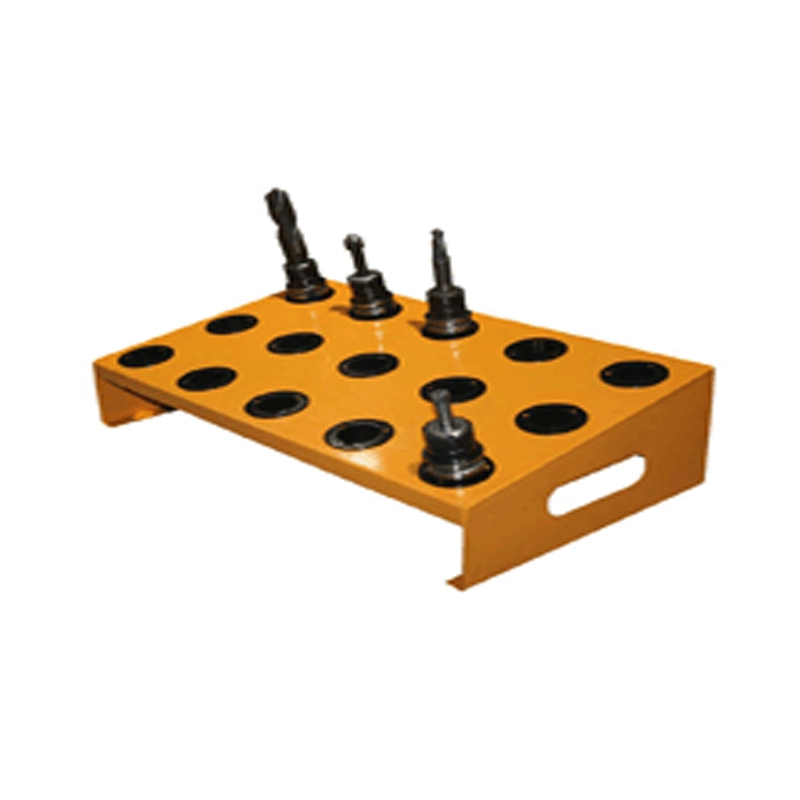
Table of Contents
Toggle🧱 1. Streamlining Granite Slab Storage & Racking
Safe, efficient handling starts with proper storage:
- Use sturdy A-frame slab racks and bundle racks that secure slabs upright to prevent toppling and damage USA Granite Tools+1mottaone.com+1Online Safety Trainer+1USA Granite Tools+1.
- Inspect racks regularly for bent supports or debris that could destabilize them mottaone.com+3wehausa.com+3OSHA+3.
- Ensure space between slabs to allow safe withdrawal—a simple design change that boosts productivity and safety.
Efficient rack layout minimizes unnecessary handling, improves access, and speeds up assembly.
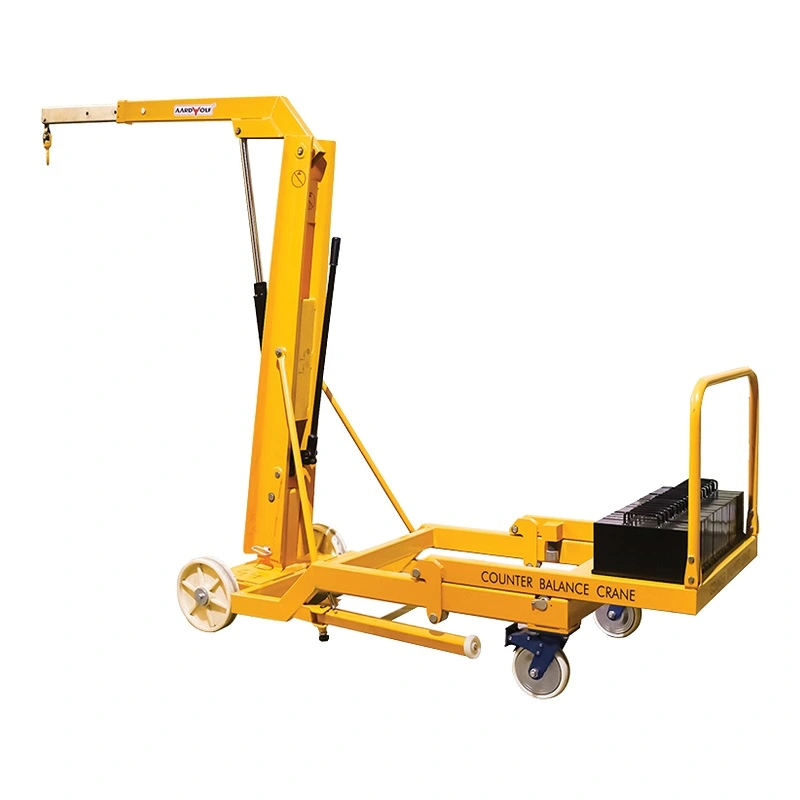
2. Loading & Unloading: Reducing Manual Labor
Manual handling of heavy granite slabs is risky and inefficient. Adopt ergonomic and mechanized solutions:
- Mechanical aids: Use overhead cranes, gantry cranes, forklifts with boom or slab-lifter attachments, scissor lifts, and vacuum lifters—this saves time and reduces injury risks houseofgranite.com+3Aardwolf America LLC+3na.bhs1.com+3Wikipedia+1Dynamic Stone Tools+1.
- Team lifting and ergonomics: When manual tasks are necessary, follow proper techniques—bend knees, maintain a neutral spine, and lift close to the body mottaone.com+1Wikipedia+1.
- Vacuum lifters: These suction-based tools stabilize and rotate slabs with minimal effort USA Granite Tools+5Aardwolf America LLC+5Dynamic Stone Tools+5.
Investing in mechanized lifts is cost-effective by reducing downtime and damage.
3. Securing & Transporting Slabs
Moving slabs within a facility or to customer sites requires precision:
- Proper fastening: Use reliable tie-downs (e.g., ratchet straps) and clamps during transit wehausa.com+1OSHA+1Wikipedia+4mottaone.com+4OSHA+4.
- Vertical transport: Always carry and load slabs vertically to reduce stress and the risk of fractures Wikipedia+5mottaone.com+5Dynamic Stone Tools+5.
- Protective packaging: Wrap slabs in foam and ballast them on A-frames or flatbeds equipped with air suspension and shock-absorbing materials for long hauls mottaone.comhouseofgranite.com.
These practices prevent unnecessary damage and streamline unloading.
4. Prioritizing Safety with Ergonomic Design
Integrating ergonomics into material handling workflows increases efficiency and worker safety:
- Use adjustable-height workstations and scissor lifts to maintain the load at waist level, reducing strain arXiv+15Wikipedia+15Dynamic Stone Tools+15.
- Redesign manual handling tasks to fit the worker’s “power zone” (mid-chest to mid-thigh) to reduce injury risk Wikipedia+1Wikipedia+1.
- Introduce job rotation, scheduled breaks, and stretch routines to reduce repetitive strain injury Wikipedia.
These simple improvements can yield significant gains in efficiency and morale.
5. Implementing Standardized Workflows & Training
Efficiency hinges on consistency and skills:
- Pre-plan workflows: Map material flow from delivery to installation—place fabrication tools logically with minimal transport in between Wikipedia.
- Train staff: Provide hands-on instruction in safe handling techniques—especially for forklift operators and slab handlers with gantry crane systems OSHAwehausa.comWikipedia.
- Develop SOPs: Written protocols should cover unloading containers, slab placement, and securing loads.
Safer, more efficient teams rely on predictable, repeatable processes.
6. Using Smart Equipment & Automation
Optimize workflows with technology:
- Material handling carts: Stone slab carts speed up movement between workstations and reduce lifting wehausa.com+2OSHA+2Online Safety Trainer+2stonefabber.comwehausa.com.
- Vacuum and mechanical lifters: Increase versatility and reduce manual handling Aardwolf America LLC.
- Overhead and gantry cranes: Essential for heavy or large-scale operations, particularly in production environments Online Safety Trainer.
Combining manual skill and automation maximizes throughput and protects workers.
7. Damage Prevention & Waste Reduction
Every damaged slab equals lost revenue:
- Edge protection: Use foam or rubber padding during handling—edges are the most vulnerable points Aardwolf America LLC+11Dynamic Stone Tools+11Online Safety Trainer+11.
- Slow, steady handling: Avoid abrupt twisting, sliding, or misalignments. Slow motions preserve slab integrity Online Safety Trainer+2Dynamic Stone Tools+2mottaone.com+2.
- Regular inspections: Monitor racks, cranes, straps, and dollies for wear to prevent accidents Aardwolf America LLC+2wehausa.com+2OSHA+2.
Well-maintained systems support consistent delivery with minimal defects.
8. Cost-Benefit of Optimized Material Handling
Investments in better handling yield long-term returns:
- Increased productivity: Faster slab movement reduces manufacturing cycle time.
- Cost savings: Fewer damaged slabs mean less waste and lower disposal costs.
- Reduced injury rates: Lowered workers’ comp and improved attendance contribute directly to your bottom line mottaone.com.
- Customization capabilities: Efficient workflows support diverse product lines—from blue pearl granite countertops to black granite countertops—with consistency.
9. Application: Granite Countertop Fabrication
Here’s how material handling improvements apply to granite countertop production:
- Receiving: Use forklifts with slab lifters to offload and place slabs on racks.
- Storage: Organize slabs by type (e.g., white granite, brown granite) on labeled racks.
- Cutting & edging: Transport slabs via carts to CNC or edging stations.
- Finishing: Move finished countertops to polishing and inspection areas with vacuum lifters.
- Delivery & installation: Load onto trucks with gantry or overhead cranes, secured by ratchet straps. Set in place at customer homes (e.g., granite countertops in [city name]) using platform cranes if needed.
This flow minimizes delays, damage, and labor intensity.
10. Summary and Best Practices
Efficient material handling for granite countertops revolves around safety, standardization, and technology:
- Use ergonomic workflows and minimize manual lifting.
- Employ mechanical aids like crane-based systems, vacuum lifters, and slab carts.
- Maintain secure packaging, proper tie-downs, and padded transport.
- Train staff thoroughly and plan layouts to reduce unnecessary movement.
- Inspect equipment routinely and embrace automation where possible.
By optimizing these areas, businesses handling natural stone—whether for granite kitchen countertops, bathroom installations, or outdoor kitchens—achieve greater efficiency, safety, and profitability.
Please log in to leave a comment.