Evaluating a material handling system is a critical process that ensures businesses are maximizing efficiency, safety, and productivity across their operations. From warehouse material handling equipment to automated material handling systems, the right evaluation approach identifies inefficiencies, reduces costs, and supports scalability.
In this guide, we’ll walk through a structured framework for assessing the performance of your material handling equipment, whether you’re operating in manufacturing, logistics, construction, or warehousing.
🔗 What Is Material Handling? Types, Equipment, Functions, Safety, and Warehouse Optimization
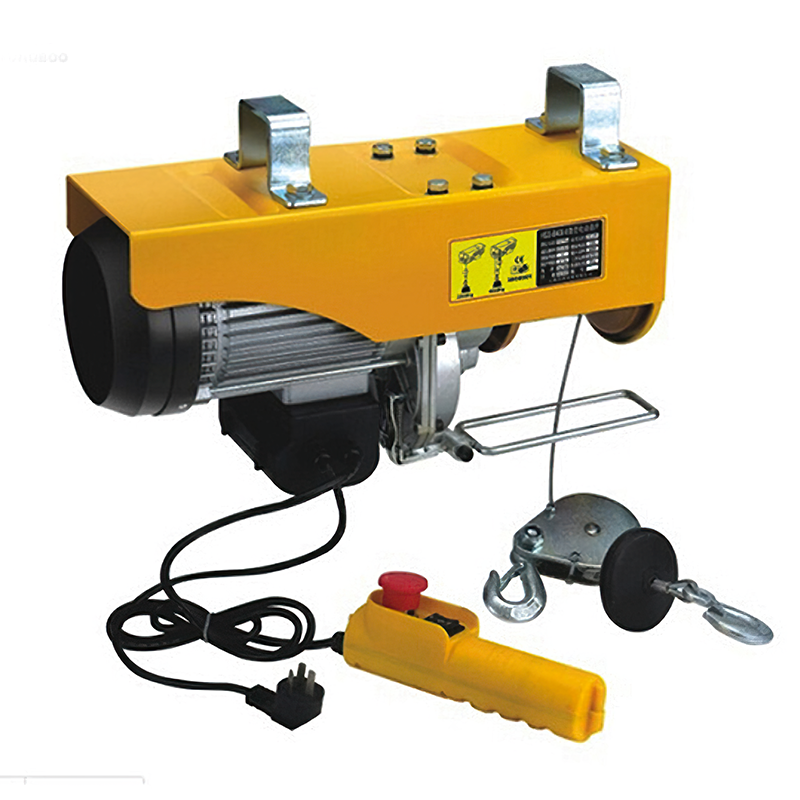
Table of Contents
ToggleWhy Evaluate a Material Handling System?
A well-optimized material handling system directly influences:
- Labor efficiency
- Safety compliance
- Operational throughput
- Storage optimization
- Cost savings
Without proper evaluation, companies risk using outdated or misaligned systems that hinder growth.
🔗 How Does Material Handling Impact the Human Labor Force?
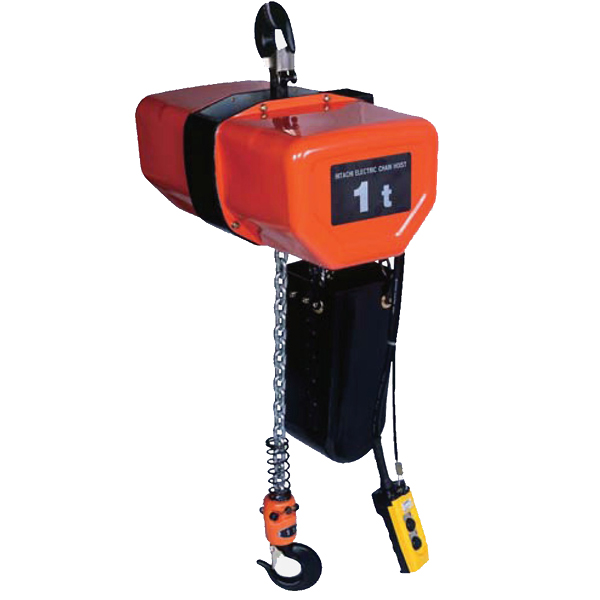
Key Criteria to Evaluate Your Material Handling System
1. Process Flow Efficiency
Begin by analyzing how materials move through your facility:
- Are materials transported in the shortest route possible?
- Is traffic flow disrupted by layout issues?
- Are workers performing unnecessary movements?
Use tools like flowcharts or simulation software to visualize inefficiencies.
2. Equipment Utilization Rates
Measure how frequently and effectively your material handling equipment is used, including:
- Forklifts for material handling
- Conveyors for material handling
- Cranes and hoists
- Overhead material handling systems
- Gantry cranes
🔗 gantry crane
Are they idle for long periods? Overloaded? Underused? Effective scheduling and real-time monitoring can help.
3. Safety and Compliance Standards
Evaluate your system against current material handling safety standards:
- Are operators properly trained?
- Is PPE available and used?
🔗 Loose Clothing Is Best to Wear When Handling Material? - Are lifting loads within acceptable weight limits?
Accidents often arise from outdated manual material handling tools or poorly configured systems.
4. Cost-Effectiveness and ROI
Consider the total cost of ownership (TCO) of your industrial material handling solutions:
- Equipment purchase or lease cost
- Maintenance and downtime
- Training and labor
For smaller operations, investing in low-cost material handling solutions like material handling carts and trolleys or vacuum lifters is often smarter than full automation.
5. Scalability and Flexibility
Can your system grow with your business?
- Bulk material handling systems should adapt to increased load sizes.
- Automated material handling systems should integrate with newer technologies like IoT and AI.
- Storage solutions must accommodate SKU expansion.
If you’re a startup or small business, consider systems that evolve affordably with minimal reinvestment.
6. Space Optimization
Evaluate your use of space:
- Are vertical racking systems utilized?
- Are aisles wide enough for forklifts and trolleys?
- Is there a mix of storage types for different materials?
Warehouse material handling equipment must be chosen to maximize cubic storage while allowing safe and efficient access.
Tools and Techniques for Evaluation
- Cycle Time Analysis: Track how long it takes to move materials from start to finish.
- Heat Mapping: Identify congestion or high-traffic areas in warehouses.
- Downtime Logs: Document equipment failures, operator delays, and transport bottlenecks.
- Lean Six Sigma Audits: Use lean principles to eliminate waste and improve flow.
Areas of Application
Material Handling for Manufacturing
- Evaluate workflows from raw materials to finished goods.
- Use modular conveyors and manual tools for flexibility.
Material Handling in Construction
- Consider terrain, mobility, and weather-resistant handling tools like paver lifters.
🔗 paver lifter
Material Handling in Food and Pharma
- Assess hygiene, temperature, and cross-contamination risks.
- Opt for stainless steel material handling carts and trolleys or sealed systems.
Logistics and Warehousing
- Examine cross-docking, inbound/outbound load balance, and RFID or barcode integration.
Optimizing Based on Your Evaluation
Once you’ve assessed the system, take action:
- Upgrade or repair underperforming equipment
- Retrain staff through material handling training programs
- Integrate automated vs manual material handling where appropriate
- Source from reliable material handling equipment manufacturers
Choosing the Right System: Key Questions
- What’s my average load size and handling frequency?
- Are materials hazardous, fragile, or temperature-sensitive?
- Can existing equipment meet future demand?
- Do I need automation or improved manual handling?
- What is my ROI threshold?
Final Thoughts
A thorough evaluation of your material handling system is essential to:
- Enhance productivity
- Improve safety
- Reduce costs
- Future-proof your operations
From heavy-duty material handling solutions to warehouse carts, every system should align with your business goals. Schedule regular audits, invest in staff training, and adapt equipment as your company evolves.
And don’t forget: an efficient material handling setup doesn’t always mean the most expensive one—it means the right one.
Please log in to leave a comment.